Cemento modificado energéticamente

Los cementos modificados energéticamente (EMC por las siglas del término inglés Energetically Modified Cement) son una clase de cementos hechos a base de puzolana (como por ejemplo, cenizas volantes, cenizas volcánicas o cenizas puzolánicas), arena silícea, escorias de alto horno o cemento Portland (o mezclas de estos elementos).[1] La denominación energéticamente modificado surge en virtud del proceso mecanoquímico aplicado a la materia prima, más precisamente clasificada como molienda de bolas de alta energía (HEBM). El proceso genera una transformación termodinámica en el material para aumentar su reactividad química.[2] El material resultante se caracteriza por ser el resultado del proceso denominado HEBM, una forma única de molienda vibratoria especial descubierta en Suecia y aplicada solo a materiales cementosos, también conocida como "Activación EMC".[3]
Al mejorar la reactividad de las puzolanas, se incrementa su capacidad de mejorar la resistencia del cemento resultante. Esto permite facilitar el cumplimiento de los requisitos mecánicos (según las "normativas técnicas") establecidas para hormigones y morteros. A su vez, esto permite la sustitución del cemento Portland en la confección de hormigones y morteros. Además, este tipo de cementos conllevan una serie de beneficios vinculados a sus cualidades a largo plazo.[2]
Los cementos modificados energéticamente tienen una amplia gama de usos. Por ejemplo, se han utilizado en hormigones para grandes proyectos de infraestructuras urbanas en Norteamérica, cumpliendo con los estándares normativos establecidos para los hormigones en los Estados Unidos.[4]
Justificación
[editar]
El término "cemento modificado energéticamente" hace referencia a una clase de cementos producidos mediante un proceso de molienda altamente intensivo especializado, descubierto en 1993 en la Universidad Tecnológica de Luleå (LTU) en Suecia.[5][6] El proceso de transformación se inicia de forma mecánica por completo, en lugar de calentar los materiales directamente.[6][7][8] Los mecanismos de las transformaciones mecanoquímicas suelen ser complejos y diferentes de los mecanismos térmicos o fotoquímicos tradicionales.[9][10] Los efectos de la transformación HEBM provocan un cambio termodinámico que reside en última instancia en la modificación de la energía de Gibbs.[11] El proceso aumenta la capacidad de unión y las tasas de reactividad química de los materiales transformados.[3][12]
El trabajo académico continuo y la investigación sobre las propiedades de "autocuración" de los cementos modificados energéticamente se continúa en la LTU.[13] Por ejemplo, la investigación en CME ha sido galardonada por la Elsa ō Sven Thysells stiftelse för konstruktionsteknisk forskning (Fundación Elsa & Sven Thysell para la Investigación en Ingeniería de la Construcción) de Suecia.[14] También se ha reconocido la contribución de los CME al dominio de la propia mecanoquímica.[15]
Uso del término "EMC"
[editar]El término "cemento modificado energéticamente" (EMC) fue utilizado por primera vez en 1992 por Vladimir Ronin, introducido en un artículo de Ronin et al. fechado en 1993 y presentado en una reunión formal del grupo académico Nordic Concrete Research.[16] El proceso fue refinado por Ronin y otros, incluido Lennart Elfgren (ahora profesor emérito de LTU).[17]
En la 45 Exposición mundial de invención, investigación e innovación, celebrada en 1996 en Bruselas, Bélgica, el EMC recibió una medalla de oro con la mención Eureka de la organización intergubernamental europea de investigación y desarrollo, por la modificación energética de cementos.[18]
El término "modificado energéticamente" se ha utilizado en otros lugares, aunque dicho uso no indica que el método utilizado fuese la activación como se define en el presente artículo.[19]
Resumen
[editar]Las propiedades reseñadas del producto, incluyen:[4][20][21][22]
- Un EMC es un polvo fino (algo típico de todos los cementos) cuyo color depende del material procesado.
- Los EMC se producen utilizando solo una "fracción" de la energía utilizada en la producción del cemento Portland (unos ~120 kWh/tonelada, menos del 10% de la energía consumida en la fabricación de cemento Portland).
- El proceso no libera CO2, y por lo tanto se trata de un producto de "emisiones cero".
- El propósito de un EMC es reemplazar el uso del cemento Portland en hormigones o morteros. Se estima que podría alcanzarse más del 70%.
- La activación de EMC es un proceso seco.
- No se liberan humos nocivos.
- La activación de EMC es un proceso de baja temperatura, aunque las temperaturas pueden ser "momentáneamente extremas" en escalas "submicrónicas".
- Los EMC no requieren productos químicos para su transformación termodinámica.
- Existen varios tipos de EMC, dependiendo de las materias primas transformadas.
- Dependiendo de los requisitos del usuario, los productos secos entregados pueden incluir también una reducida proporción de cemento Portland de "alto contenido de clinker".
- Cada tipo de EMC tiene sus propias características de rendimiento, incluida la resistencia mecánica y el desarrollo de esta resistencia. Los hormigones confeccionados a partir de EMC pueden producir importantes capacidades de "autocuración".
- Los EMC más utilizados están hechos de cenizas volantes y puzolanas naturales. Estos son materiales relativamente abundantes y las características de rendimiento pueden superar a las del cemento Portland.
- La arena de sílice y el granito también se pueden tratar mediante el proceso para reemplazar al cemento Portland.
- Los productos de EMC han sido ampliamente probados por laboratorios independientes y certificados para su uso por varios DOT de EE. UU., incluso en proyectos de la Administración Federal de Carreteras.
- Los EMC cumplen con los estándares técnicos respectivos, como ASTM C618-19 (EE. UU.); EN-197, EN-206 y EN 450-1:2012 (territorios del Comité Europeo de Normalización, incluido el Espacio Económico Europeo); BS 8615‑1:2019 (Reino Unido).
- En comparación con el uso de cemento Portland, los hormigones confeccionados con EMC no requieren un "contenido de cemento total" más alto para cumplir con los requisitos de desarrollo de resistencia.
- En las pruebas realizadas por BASF, el desarrollo de resistencia a los 28 días cuando se sustituye el 55% del cemento Portland por un EMC puzolánico natural fue de 14.000 psi/96,5 MPa (es decir, > C95), con un "contenido de cemento total" de 335 kg/m^3 (564 lbs/CY) de la mezcla del hormigón.
El EMC como cemento de bajas emisiones
[editar]A diferencia del cemento Portland, la producción de EMC no genera dióxido de carbono en absoluto. Esto hace que los EMC sean "cementos bajos en carbono".[7]
Las primeras afirmaciones citadas sobre las capacidades de reducción de CO2 del EMC se realizaron en 1999, cuando la producción mundial de cemento Portland era de 1600 millones de toneladas por año.[20][23] De 2011 a 2019, la producción mundial de cemento Portland aumentó de 3600 a 4100 millones de toneladas por año.[24][nota 1] El potencial del cemento modificado energéticamente para contribuir a una reducción mundial de CO2 ha sido reconocido externamente desde 2002 y continúa.[5][6][8] El reconocimiento reciente ha incluido el informe de la Comisión para la Transición Energética (redactado bajo la dirección de Adair Turner y Nicholas Stern) Posible misión de enfoque sectorial: cemento (2019).[25] El reconocimiento del potencial de "carbono cero" fue establecido por McKinsey & Co en su informe de 2020 "Estableciendo las bases para el cemento sin carbono".[26] En 2023, la contribución que ofrecen los EMC para lograr materiales "bajos en carbono" fue reconocida aún más dentro del dominio académico de la mecanoquímica.[15]
Producción y aplicaciones
[editar]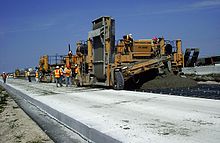
Sin emisiones nocivas ni productos químicos tóxicos durante la producción
[editar]La activación de EMC es un proceso puramente mecánico. Como tal, no implica calentar ni quemar ni, de hecho, ningún tratamiento químico. Esto significa que no se producen humos durante su fabricación.[20]
Historial de uso
[editar]Los EMC se han producido para su empleo en diversos proyectos desde 1992.[4] En 2010, el volumen de hormigón vertido que contenía EMC fue de aproximadamente 4.500.000 yardas cúbicas (3.440.496 m3), principalmente en proyectos del DOT de EE. UU.[4] Para poner este dato en contexto, supone un volumen superior al de toda la construcción de la presa Hoover (incluidas sus plantas de energía asociadas y obras anexas), donde se vertió un total de 4.360.000 yardas cúbicas (3.333.459 m³) de hormigón, equivalente a una carretera estándar de EE. UU. desde San Francisco a la ciudad de Nueva York.[27]
Uso temprano en Suecia
[editar]Uno de los primeros proyectos que utilizó EMC a partir de cenizas volantes fue la construcción de un puente de carretera en Karungi, Suecia, en 1999, con la empresa constructora sueca Skanska. El puente vial de Karungi ha resistido los duros inviernos de Karungi y las fuertes oscilaciones de temperatura diurnas a lo largo del año.[20]
Uso en los Estados Unidos
[editar]En los Estados Unidos, los cementos modificados energéticamente han sido aprobados para su uso por varias agencias estatales de transporte, incluidas las de Pensilvania, Texas y California.[22]
En los Estados Unidos, se han construido puentes de carreteras y cientos de kilómetros de pavimentación de carreteras con hormigones fabricados con EMC derivados de cenizas volantes.[4] Estos proyectos incluyen secciones de la Interestatal 10.[4] En estos proyectos, el EMC reemplazó al menos el 50% del cemento Portland en el hormigón vertido.[28] Esto es aproximadamente 2,5 veces más que la cantidad típica de cenizas volantes en proyectos donde no se usan cementos modificados energéticamente.[29] Los datos de pruebas independientes mostraron que se excedieron los requisitos de desarrollo de resistencia a los 28 días en todos los proyectos.[28]
Otro proyecto fue la ampliación de las terminales de pasajeros en el puerto de Houston, Texas, donde la capacidad del cemento modificado energéticamente para producir hormigones con altas resistencias a la permeabilidad iónica de cloruros y sulfatos (es decir, mayor resistencia al agua de mar) fue un factor determinante.[4]
Propiedades de hormigones y morteros elaborados a partir de EMCs
[editar]
Diseño particularizado según su uso final
[editar]El comportamiento de los morteros y hormigones elaborados a partir de EMC se puede diseñar a medida. Por ejemplo, los hormigones EMC pueden variar desde aplicaciones generales (según su resistencia y durabilidad), hasta la producción de cementos de endurecimiento rápido y ultrarrápido para hormigones de alta resistencia (por ejemplo, más de 70 MPa/10 150 psi en 24 horas y más de 200 MPa/29 000 psi a los 28 días).[21] Esto permite que los cementos energéticamente modificados puedan utilizarse en hormigones de alto rendimiento.[21]
Durabilidad de hormigones y morteros EMC
[editar]Es probable que cualquier material cementoso que se someta a la activación de EMC presente una mayor durabilidad, incluido el cemento Portland tratado con activación de EMC.[21] En cuanto a los EMC puzolánicos, los hormigones elaborados con EMC puzolánicos son más duraderos que los hormigones elaborados con cemento Portland.[31]
El tratamiento del cemento Portland con activación EMC produce hormigones de altas prestaciones, incluyendo alta resistencia, elevada durabilidad y un desarrollo de la resistencia más rápido que los hormigones producidos con cemento Portland sin tratar.[21] El tratamiento del cemento Portland con el proceso de activación de EMC puede aumentar el desarrollo de su resistencia en casi un 50%, y también mejorar significativamente su durabilidad, medida según los métodos generalmente aceptados.[21][30]
Mayor resistencia al ataque del agua salada
[editar]El hormigón fabricado con cemento Portland ordinario sin aditivos tiene una resistencia relativamente baja al agua salobre.[30] Por el contrario, los EMC muestran una alta resistencia al ataque iónico de cloruros y sulfatos, junto con un baja reactividad álcali-sílice.[28] Por ejemplo, se han realizado pruebas de durabilidad según el "método Bache" (véase el diagrama). Muestras de hormigón con resistencias a la compresión respectivas de 180,3 y 128,4 MPa (26.150 y 18.622 psi) después de 28 días de curado, se probaron usando el método de Bache. Las muestras estaban hechas de (a) EMC (que comprende cemento Portland y humo de sílice, ambos sometidos a activación de EMC) y (b) cemento Portland. La pérdida de masa resultante se representó gráficamente para determinar la durabilidad. Como comparación, los resultados de la prueba mostraron:
- Considerando que el hormigón de cemento Portland de referencia tuvo "destrucción total después de unos 16 ciclos del método de Bache, en línea con las propias observaciones de Bache para el hormigón de alta resistencia";[21][30]
- El hormigón de alto rendimiento EMC mostró una "durabilidad constante de alto nivel" durante todo el período de prueba de 80 ciclos de Bache, por ejemplo, "prácticamente no se ha observado incrustación en el hormigón".[21]
En otras palabras, el tratamiento del cemento Portland con el proceso de activación de EMC puede aumentar el desarrollo de resistencia en casi un 50% y también mejorar significativamente su durabilidad, medida de acuerdo con los métodos generalmente aceptados.[21]
Baja lixiviabilidad de los hormigones con EMC
[editar]La Universidad Tecnológica de Luleå realizó pruebas de lixiviación en 2001 en Suecia, en nombre de una empresa de producción de energía sueca, en un hormigón confeccionado con un EMC hecho de cenizas volantes. Estas pruebas confirmaron que el hormigón "mostró una lixiviabilidad específica de superficie baja" con respecto a "todos los metales ambientalmente relevantes".[32][33]
EMC que utilizan puzolanas como materiales volcánicos
[editar]
-
FOTO A[34]
-
FOTO B
Propiedades de autorreparación de los EMC puzolánicos
[editar]Las reacciones puzolánicas naturales pueden provocar que los morteros y hormigones que contienen estos materiales se "autorreparen".[35][36][37] El proceso de activación de EMC puede aumentar la probabilidad de que ocurran estas reacciones puzolánicas.[38][39] Se ha observado y estudiado la misma tendencia en las diversas estructuras de soporte de la basílica de Santa Sofía construidas en la época del emperador bizantino Justiniano I (actualmente en Estambul, Turquía).[40] Allí, al igual que en el caso de la mayoría de los cementos romanos, se utilizaron morteros que contenían altas cantidades de ceniza puzolánica, para obtener una mayor resistencia a las tensiones generadas en las edificaciones por los terremotos.[41]
Los EMC fabricados con materiales puzolánicos exhiben capacidades de autorreparación "biomiméticas" que se pueden fotografiar a medida que se desarrollan (véanse las imágenes adjuntas).[34]
EMC que utilizan puzolanas de California
[editar]Los hormigones fabricados reemplazando al menos el 50% del cemento Portland con EMC han dado resultados prácticos consistentes en aplicaciones de alto volumen.[28] Este también es el caso del EMC producido a partir de puzolanas naturales (como por ejemplo, cenizas volcánicas).[42]
Los depósitos de cenizas volcánicas del sur de California se probaron de forma independiente. Sustituyendo al 50% el cemento Portland en la dosificación, los hormigones resultantes excedieron los requisitos del estándar ASTM correspondiente.[43] A los 28 días, su resistencia a compresión fue de 4180 psi / 28,8 megapascales (N/mm²). La resistencia a los 56 días superó los requisitos para el hormigón de 4500 psi (31,1 MPa), incluso teniendo en cuenta el margen de seguridad recomendado por el American Concrete Institute.[44] El hormigón fabricado de esta manera era trabajable y suficientemente fuerte, excediendo el estándar del 75% de actividad puzolánica tanto a los 7 días como a los 28 días.[43] También aumentó la lisura superficial de las puzolanas en el hormigón.[43]
Efecto sobre las reacciones puzolánicas
[editar]
La activación de EMC es un proceso que aumenta la afinidad química de una puzolana.[38][39] Esto conduce a un desarrollo de resistencia mayor y más rápido del hormigón resultante, en proporciones de reemplazo más altas que las puzolanas no tratadas.[28][42] Estas puzolanas transformadas (altamente reactivas) demuestran beneficios adicionales al utilizar formas de reacción puzolánica conocidas que generalmente tienen como su objetivo final una gama de productos hidratados. Un estudio de resonancia magnética nuclear sobre muestras de EMC concluyó que su activación provocó "la formación de capas delgadas de SiO2 alrededor de los cristales de C3S", que a su vez "acelera la reacción puzolánica y promueve el crecimiento de redes más extensas de sustancias hidratadas".[45]
En términos simples, mediante el uso de puzolanas en el hormigón, la portlandita porosa (reactiva) se puede transformar en compuestos duros e impermeables (relativamente no reactivos), en lugar del carbonato cálcico relativamente reactivo, poroso y blando, generado con el cemento ordinario.[46] Muchos de los productos finales de la química puzolánica exhiben una dureza superior a 7,0. Las capacidades de "autorreparación" también pueden contribuir a mejorar la durabilidad en aquellas aplicaciones en las que deban soportarse esfuerzos de tracción.
En mayor detalle, los beneficios del hormigón puzolánico comienzan con la comprensión de que en los hormigones convencionales, el cemento Portland se combina con el agua para producir un material similar a la piedra a través de una serie compleja de reacciones químicas, cuyos mecanismos aún no se conocen por completo. El proceso, denominado hidratación mineral, forma dos compuestos cementantes en el hormigón: silicato cálcico hidratado (C-S-H) y hidróxido de calcio (Ca(OH)2). Esta reacción se puede producir de tres maneras:[47]
- Proceso estándar:
- Proceso de equilibrio:
- Química del cemento (el guion denota la variable estequiométrica): C3S + H → C-S-H + CH
La reacción de hidratación subyacente forma dos productos:
- Silicato cálcico hidratado (C-S-H), que le da al hormigón su resistencia y estabilidad dimensional. La estructura cristalina del C-S-H en la pasta de cemento aún no se ha resuelto por completo y todavía hay un debate en curso sobre su nanoestructura.[48]
- Hidróxido de calcio (Ca(OH)2), que en la química del hormigón también se conoce como portlandita. En comparación con el silicato cálcico hidratado, la portlandita es relativamente porosa, permeable y blanda (2 a 3, en la escala de Mohs).[49] También es séctil, formando laminillas de exfoliación flexibles.[50] La portlandite es soluble en agua, produciendo una solución alcalina que puede comprometer la resistencia del hormigón al ataque de elementos ácidos.[31]
La portlandita constituye alrededor del 25% del hormigón confeccionado con cemento Portland sin materiales cementosos puzolánicos.[46] En este tipo de hormigón, el dióxido de carbono se absorbe lentamente para convertir la portlandita en carbonato cálcico insoluble (CaCO3), en un proceso llamado carbonatación:[46]
En forma mineral, el carbonato cálcico puede exhibir una amplia gama de dureza dependiendo de cómo se forme. En su forma más blanda, se puede formar en el hormigón como creta (de dureza 1,0 en escala de Mohs). Al igual que la portlandita, el carbonato cálcico en forma mineral también puede ser poroso, permeable y con poca resistencia al ataque de los ácidos, lo que hace que libere dióxido de carbono.
Sin embargo, los hormigones puzolánicos, incluidos los EMC, continúan consumiendo la portlandita blanda y porosa a medida que continúa el proceso de hidratación, convirtiéndola en hormigón endurecido adicional como silicato cálcico hidratado (C-S-H) en lugar de carbonato cálcico.[46] Esto da como resultado un hormigón más denso, menos permeable y más duradero.[46] Se trata de una reacción ácido-base entre la portlandita y el ácido silícico (H4SiO4) que se puede representar de la siguiente manera:[51]
Además, muchas puzolanas contienen aluminato (Al(OH)4−) que reaccionará con la Portlandita y el agua para formar:
- Aluminato de calcio hidratado, como el granate de aluminio y calcio (hidrogrosularia: C4AH13 o C3AH6 en notación química del cemento, dureza de 7,0 a 7,5 en la escala de Mohs);[52] o
- En combinación con la sílice, para formar strätlingita (Ca2Al2SiO7''·8H2O o C2ASH8 en notación química del cemento), que en términos geológicos puede formarse como xenolito en los basaltos como caliza metamórfica.[53]
La química del cemento puzolánico (junto con la química del cemento con alto contenido de aluminato) es compleja y no queda necesariamente restringida a las vías anteriores. Por ejemplo, la strätlingita se puede formar de varias maneras, incluida la siguiente ecuación que puede aumentar la resistencia de un hormigón:[54][55]
El papel de las puzolanas en la química del hormigón no se comprende completamente. Por ejemplo, la strätlingita es metaestable, que en un entorno de alta temperatura y contenido de agua (que se puede generar durante las primeras etapas de curado del hormigón) puede producir por sí mismo partículas de granate de calcio y aluminio estables (véase el primer punto anterior).[58] Este proceso se puede representar mediante la siguiente ecuación:
- 3C2AH8 → 2C3AH6 + AH3 + 9H ; (notación química del cemento)[59]
Según el primer punto, aunque la inclusión de granate de calcio y aluminio en sí no es problemática, si en cambio se produce por la vía anterior, entonces pueden producirse microfisuras y pérdida de resistencia en el hormigón.[60] Sin embargo, la adición de puzolanas de alta reactividad a la mezcla de hormigón evita tal reacción de conversión.[61]
En resumen, mientras que las puzolanas proporcionan varias posibilidades químicas para formar materiales endurecidos, las puzolanas de "alta reactividad" como la escoria de alto horno (GGBFS) también pueden estabilizar alguno de estos procesos. En este contexto, se ha demostrado que los EMC fabricados a partir de cenizas volantes producen hormigones que cumplen las mismas características que los hormigones que contienen "escoria 120" (es decir, GGBFS) según la norma estadounidense ASTM C989.[28][62]
La portlandita, cuando se expone a bajas temperaturas, condiciones de humedad y condensación, puede reaccionar con los iones sulfato, produciendo eflorescencias. Por el contrario, la química puzolánica aminora la cantidad de portlandita disponible para reducir la generación de eflorescencias.[63]
Activación EMC
[editar]
El propósito de la activación de EMC es fundamentalmente causar la destrucción de la estructura cristalina del material procesado, para convertirlo en un material amorfo.[38] Aunque este cambio aumenta la reactividad química del material procesado, no se produce ninguna reacción química "durante" el proceso de activación de EMC.
En su forma más simple, la mecanoquímica puede definirse como "un campo que estudia las reacciones químicas iniciadas o aceleradas por la absorción directa de energía mecánica".[15] Más técnicamente, se puede definir como una rama de la química que se ocupa de la "transformación química y fisicoquímica de sustancias en todos los estados de agregación producida por el efecto de la energía mecánica".[65] La IUPAC no contiene una definición estándar del término "mecanoquímica", sino que define una ""reacción" mecanoquímica" como una reacción química "inducida por la absorción directa de energía mecánica", al tiempo que señala "corte, estiramiento y molienda son métodos típicos para la generación mecano-química de propiedades reactivas".[66][67]
Más estrictamente, activación mecánica fue un término definido por primera vez en 1942 como un proceso que implica un aumento en la capacidad de reacción de una sustancia que permanece químicamente sin cambios.[68] Aún más estrictamente, la activación de EMC es una forma especializada de activación mecánica limitada a la aplicación de molienda de bolas de alta energía (HEBM) a materiales cementosos. De manera más restringida, la activación de EMC implica el uso de pulverización vibratoria, y usando exclusivamente sus propios medios de molienda.[38] Como se indica en un libro de texto académico de 2023 limitado a la mecanoquímica, la activación de EMC ha "demostrado de manera impresionante" sus efectos al provocar un cambio en la reactividad del material de cemento alternativo y las características físicas resultantes del hormigón.[15]
Justificación termodinámica
[editar]Más concretamente, el proceso HEBM puede describirse como un aumento de la reactividad química de un material al incrementar su energía "potencial" química. En la activación de EMC, la energía mecánica transferida se almacena en el material como defectos provocados por la destrucción de la estructura cristalina del material. Por lo tanto, el proceso transforma el estado de sustancias sólidas en otros estados termodinámica y estructuralmente más "inestables", lo que permite una explicación de esa mayor reactividad como un aumento de su energía de Gibbs:[69]
- donde para la temperatura , los términos y son los valores de Gibbs respectivos del material procesado y sin procesar.
En su forma más simple, el proceso HEBM provoca la destrucción de los enlaces cristalinos para aumentar la reactividad de un material.[70] Desde la perspectiva termodinámica, cualquier reacción química posterior puede disminuir el nivel de exceso de energía en el material activado (es decir, como reactivo) para producir nuevos componentes que comprendan una energía química más baja y una estructura física más estable. Por el contrario, para convertir el material preprocesado en un estado físico más reactivo, el desorden generado durante el proceso HEBM puede justificarse como equivalente a una "descristalización" (y, por lo tanto, un aumento de entropía) que en parte produce un aumento de volumen (por la disminución de la densidad aparente). Un proceso inverso, a veces llamado "relajación", puede ser casi inmediato (10−7 a 10−3 segundos) o tardar mucho más (por ejemplo, 106 segundos).[71] En última instancia, cualquier efecto termodinámico general "retenido" puede justificarse sobre la base de que cualquier proceso "inverso" de este tipo es incapaz de alcanzar un estado final termodinámico ideal por sí solo. Como resultado, en el curso de la activación mecánica de los minerales, los procesos de "relajación" inversa no pueden disminuir por completo la energía libre de Gibbs que se ha creado. Por lo tanto, la energía permanece en el material, que se almacena en los "defectos" creados en la red cristalina.[72][73]
Efecto termodinámico neto del proceso HEBM
[editar]En general, el proceso HEBM genera un efecto termodinámico neto:[74][75][76]
- El desorden estructural implica un aumento tanto de la entropía como de la entalpía y, por lo tanto, estimula las propiedades del cristal según las modificaciones termodinámicas. Solo una pequeña fracción (aproximadamente el 10%) del exceso de entalpía del producto activado puede considerarse como aumento del área superficial.
- En cambio, la mayor parte del exceso de entalpía y las propiedades modificadas pueden atribuirse principalmente al desarrollo de estados termodinámicamente inestables en la red del material (y no como una reducción del tamaño de las partículas).
- Dado que el sistema activado es inestable, el proceso de activación es reversible, lo que da como resultado la desactivación, la recristalización, la pérdida de entropía y la producción de energía por parte del sistema. Ese proceso inverso ("relajación") continúa hasta un equilibrio termodinámico, pero finalmente nunca puede alcanzar una estructura ideal (es decir, una libre de defectos).
- Una descripción más completa de un proceso de "activación" de este tipo incluye también la entalpía, mediante la cual, según la ecuación de Gibbs-Helmholtz, la energía libre de Gibbs entre el estado sólido activado y el no activado se puede representar como:
- donde, es el cambio de entalpía y el cambio de entropía.
Alteración cristalina resultante
[editar]Donde el desorden en los cristales es bajo, es muy pequeño (si no despreciable). Por el contrario, en cristales muy deformados y desordenados, los valores de pueden tener un impacto significativo en la energía libre de Gibbs generada.
Dejando a un lado el calor generado durante el proceso debido a efectos ocasionados durante el proceso de activación como la fricción, el exceso de energía libre de Gibbs retenida en el material activado puede justificarse debido a dos cambios, a saber, un aumento en el área de superficie específica (), y de los defectos de la estructura cristalina ().[77][76] En procesos HEBM exitosos como la activación de EMC:[78][79]
- En cuanto a (), solo alrededor del 10% del exceso de energía de dicho producto activado puede contabilizarse como un cambio en el área superficial.
- En cuanto a (), casi toda la energía acumulada está contenida en los defectos estructurales reales del material procesado.
Una aproximación a la activación de EMC
[editar]El valor relativamente bajo de () en comparación con el elevado valor de () sirve para distinguir aún más el proceso HEBM de la molienda en general o "fresado" (donde, en cambio, el único objetivo es aumentar el área de superficie de los materiales procesados), lo que permite obtener una explicación del cambio en la entropía del material pulverizado en forma de energía elástica (almacenada en defectos de la red cristalina que pueden tardar años en "relajarse"), que es la "fuente del exceso de energía y entalpía de Gibbs".[77] En cuanto a la entalpía , se pueden reseñar cuatro descriptores para dar una visión general del cambio total durante dicho proceso de activación:[78][80][81]
- donde:
- es una medida de la densidad de dislocación;
- es una medida de nuevas fases (transformación polimórfica);
- es una medida de la formación de material amorfo;
- es una medida de la superficie específica.
- donde:
Debido a que la mayor parte de la energía que se requiere durante el proceso de activación de EMC es absorbida por (), es trivial. Por lo tanto, las principales funciones para el cambio de entalpía se aproximan a:
En la activación de EMC, los términos anteriores y se consideran particularmente destacables debido a la naturaleza de los cambios observados en la estructura física.[38] Por lo tanto, el cambio en la entalpía ocasionado durante la activación de EMC se puede aproximar a:[80][81]
- es decir,
- donde:
- , , y corresponden respectivamente al volumen molar del material, al vector de Burgers, al módulo de cizalladura y a la densidad de dislocación;[80][81]
- y son respectivamente la concentración de la energía de amorfización molar y de la fase amorfa.[80][81]
Reactividad a baja temperatura
[editar]A partir de la construcción termodinámica anterior, la activación de EMC da como resultado una fase altamente "amorfa" que puede justificarse como un gran aumento de y también un gran aumento de .[38][80][81] Los beneficios de la activación de EMC son grandes en , lo que significa que su reactividad depende menos de la temperatura. En términos del ímpetu termodinámico de cualquier reacción, la entalpía general de un reactivo no depende de la temperatura , lo que significa que un material que se sometió a HEBM con una elevación correspondiente de puede reaccionar a una temperatura más baja (ya que el reactivo "activado" depende menos de la temperatura para su progresión). Además, la reacción de un EMC puede exhibir mecanismos físicos a escalas extremadamente pequeñas "con la formación de capas delgadas de SiO2", con la sugerencia de que la activación de EMC aumenta la proporción de zonas de reacción favorables.[45] Otros estudios han determinado que el proceso HEBM puede reducir significativamente la temperatura requerida para que se produzca una reacción posterior (hasta una reducción de tres veces), por lo que un componente principal de la dinámica de reacción general se inicia en una "fase nanocristalina o amorfa" para exhibir "valores inusualmente bajos o incluso negativos de la energía de activación aparente" necesarios para provocar una reacción química.[82]
En general, es probable que los EMC dependan menos de la temperatura para la progresión de una vía química (véase la sección anterior sobre reacciones puzolánicas), lo que puede explicar por qué los EMC brindan beneficios de "autorreparación" incluso a las bajas temperaturas registradas en el Ártico.[83][84]
Justificación física (amorfización)
[editar]Los grandes cambios en , más particularmente en los valores resultantes de y , brindan una idea de la eficacia de la activación de EMC. La amorfización del material cristalino en condiciones de alta presión "es un fenómeno bastante inusual" por la sencilla razón de que "la mayoría de los materiales en realidad experimentan la transformación inversa de amorfos a cristalinos en condiciones de alta presión".[85] La amorfización representa una "periodicidad" altamente distorsionada del elemento reticular de un material, que comprende una energía libre de Gibbs relativamente alta.[72][74] De hecho, la amorfización puede compararse con un estado "casi-fundido".[73][75]
En total, al igual que otros procesos HEBM, la activación de EMC provoca la destrucción cristalina debido a factores extremadamente violentos y perturbadores que se producen en la nanoescala del material que se procesa.[86] Aunque son de corta duración y altamente focales, los procesos se repiten a alta frecuencia: por lo tanto, se cree que esos factores imitan las presiones y temperaturas que se encuentran en las profundidades de la Tierra para causar el cambio de fase requerido.[2] Por ejemplo, Peter Thiessen desarrolló el "modelo de magma-plasma" que supone que se pueden generar temperaturas localizadas (superiores a 103 Kelvin) en los diversos puntos de impacto para inducir un estado de plasma excitado momentáneo en el material, caracterizado por la eyección de electrones y fotones junto con la formación de fragmentos excitados (véase el diagrama de arriba).[87] Los datos experimentales recopilados desde 1975 de la generación de grietas localizadas, en sí mismo un componente importante de la activación de EMC, han confirmado temperaturas elevadas en este proceso.[88]
Molinos vibratorios de bolas (MVB)
[editar]Para la activación de EMC, el método HEBM utilizado es un molino de bolas vibratorio (MVB).[38] Un MVB utiliza un mecanismo de accionamiento excéntrico vertical para hacer vibrar una cámara cerrada hasta muchos cientos de ciclos por minuto. La cámara se llena con el material que se procesa junto con objetos especializados llamados "medios de molienda". En su formato más simple, estos medios pueden ser simples bolas hechas de cerámica especial. En términos prácticos, la activación de EMC despliega diversos medios de molienda de diferentes tamaños, formas y compuestos para lograr la transformación mecanoquímica requerida.[4]
Se ha sugerido que un MVB triturará entre 20 y 30 veces más que un molino de bolas rotatorio, lo que refleja que el mecanismo de un MVB es especialmente eficaz.[89]
Cinética del molino vibratorio de bolas
[editar]En términos simples, la fuerza de compresión que actúa entre dos bolas "idénticas" que chocan en un MVB se puede expresar como:[90]
- donde
- y donde es la masa de ambas bolas, su radio, la velocidad absoluta de impacto y el módulo de Young del material de las bolas.[90]
Se puede ver que un aumento en la velocidad de impacto incrementa . El tamaño y la masa de los medios de molienda también contribuyen a la eficacia del proceso. El término denominador de incorpora , lo que significa que la naturaleza del material utilizado para los medios de molienda es un factor importante ( finalmente se eleva al cuadrado en , por lo que su valor negativo no tiene ninguna consecuencia). Más fundamentalmente, debido a la rápida vibración, se imparte una alta aceleración a los medios de molienda, con lo que los impactos continuos, breves y agudos sobre el cemento dan como resultado una rápida reducción del tamaño de las partículas.[89] Además, las altas presiones y la tensión cortante facilitan la transición de fase requerida a un estado amorfo tanto en el punto de impacto como durante la transmisión de ondas de choque que pueden producir presiones incluso mayores que el propio impacto.[86]
Por ejemplo, el tiempo de contacto de una colisión de dos bolas puede ser tan corto como 20 μs, generando una presión de 3,3 GPa hacia arriba y con un aumento de la temperatura ambiente asociado de 20 Kelvin.[86] Debido a la corta duración del impacto, la tasa de cambio en cantidad de movimiento es significativa, generando una onda de choque de una duración de solo 1-100 μs pero con una presión asociada de 10 GPa hacia arriba y una temperatura focal y muy localizada (es decir, a escala nanoscópica) hasta varios miles de grados Kelvin.[86] Para poner esto en contexto, una presión de 10 GPa equivale a la ejercida por unos 1.000 kilómetros de agua de mar. Como otro ejemplo, el impacto de dos bolas de acero idénticas de 2,5 cm de diámetro con una velocidad de 1 m/s generará una colisión con una densidad de energía de más de 109 julios/m2; y con bolas de alúmina de los mismos 2,5 cm de diámetro y una velocidad de 1 m/s se genera una densidad de energía aún mayor.[90] Las colisiones ocurren en una escala de tiempo muy corta y, por lo tanto, la "tasa de liberación de energía sobre el área de contacto relativamente pequeña puede ser muy alta".[90]
Véase también
[editar]Antecedentes científicos de la activación de EMC:
Notas
[editar]- ↑ Dos aspectos: (I) 2011 La producción mundial de cemento Portland fue de aproximadamente 3.600 millones de toneladas según los datos del Servicio Geológico de Estados Unidos (USGS) (2013), un dato razonablemente preciso. Debe tenerse en cuenta también que, según el mismo informe, para 2012 se estimó que la producción mundial de cemento Portland aumentaría a 3.700 millones de toneladas (un aumento de 100 millones de toneladas año tras año), cuando en realidad la cifra real para 2012 fue de 3.800 millones de toneladas. (II) Estimación del total mundial de producción de CO2 en 2011: 33.376 millones de toneladas (sin transporte internacional). Fuente: U.E. Comisión Europea, Centro Común de Investigación (JRC)/PBL (Agencia de Evaluación Ambiental de los Países Bajos); Base de datos de emisiones para la investigación atmosférica global (EDGAR), versión 4.2. Se estimaron las tendencias de 2009-2011 para los sectores relacionados con la energía según el consumo de combustibles fósiles para 2009-2011 a partir de la Revisión de la energía mundial 2011 (BP, 2012), para la producción de cemento según datos preliminares del USGS (2012), a excepción de China, para el que se hizo uso de los datos de la Oficina Nacional de Estadísticas de China (NBS) (2009, 2010, 2011).
[A partir de mayo de 2013, véase EDGAR, sección de enlace externo]. - ↑ El "método de Bache" para probar la durabilidad del hormigón simula las variaciones diarias de temperatura en salmuera. Puede usarse la Prueba 1 o la Prueba 2, o realizarse secuencialmente durante 48 horas. El método induce la saturación con agua conteniendo un 7,5% de sal (es decir, una concentración más alta que la del agua de mar), seguida de congelación o calentamiento en un ciclo de 24 horas para simular rangos de temperatura diurnos altos. El ciclo elegido se repite hasta el agotamiento para determinar la pérdida de masa. Por lo tanto, el método de Bache se acepta generalmente como uno de los procedimientos de prueba más severos para el hormigón para determinar su durabilidad.
- ↑ La foto grande muestra una viga de prueba de concreto hecha con un EMC sometido a flexión de 3 puntos RILEM en la Universidad Tecnológica de Luleå en Suecia (febrero de 2013). Este tratamiento induce grietas para probar las propensiones a la "autorreparación". Se utilizó hormigón (cemento total: 350 kg/m³) que contenía un 40% de cemento Portland y un 60% de EMC a partir de cenizas volantes. FOTO A: Se indujeron grietas de un ancho promedio de 150-200 μm después de aproximadamente 3 semanas de curado con agua. FOTO B: Sin ninguna intervención, el hormigón puzolánico de alto volumen exhibió el relleno gradual de las grietas con gel CSH recién sintetizado (un producto de la reacción puzolánica en curso). Las grietas se rellenaron por completo después de unos 4,5 meses. Durante el período de observación, también se registró un desarrollo continuo de la resistencia en virtud de la reacción puzolánica en curso. Este proceso, junto con las propiedades de "autorreparación" observadas, tiene un impacto positivo en la durabilidad del hormigón. Todas las fotos Dr. V. Ronin y The Nordic Concrete Federation.
- ↑ Notas adicionales sobre química puzolánica: (A) La relación Ca/Si (o C/S) y el número de moléculas de agua pueden variar, al igual que la estequiometría C-S-H. (B) A menudo, los cristales hidratados se forman, por ejemplo, cuando el aluminato tricálcico reacciona con el sulfato de calcio disuelto para formar hidratos cristalinos (3CaO·(Al,Fe)2O3·CaSO4·nH2O, fórmula general simplificada). Esto se denomina fase AFm ("alúmina, óxido férrico, monosulfato"). (C) La fase AFm per se no es excluyente. Por un lado, mientras que los sulfatos, junto con otros aniones como carbonatos o cloruros pueden sumarse a la fase AFm, también pueden causar una fase AFt donde se forma ettringita (6CaO·Al2O3·3SO3·32H2O o C6S3H32). (D) Generalmente, la fase AFm es importante en el proceso de hidratación posterior, mientras que la fase AFt puede ser la causa del fallo del hormigón conocida como DEF, que puede ser un problema particular en hormigones no puzolánicos (véase, por ejemplo, Folliard, K., et al., Preventing ASR/ DEF en hormigón nuevo: Informe final, TXDOT y FHWA de EE. UU.: Doc. FHWA/TX-06/0-4085-5, Rev. 06/2006). (E) Se cree que las vías químicas puzolánicas que utilizan iones Ca2+ hacen que la ruta AFt sea relativamente suprimida.
Referencias
[editar]- ↑ Mark Anthony Benvenuto (24 de febrero de 2015). Industrial Chemistry: For Advanced Students. De Gruyter. pp. 134-. ISBN 978-3-11-035170-5.
- ↑ a b c Tole, Ilda; Habermehl-Cwirzen, Karin; Cwirzen, Andrzej (1 de agosto de 2019). «Mechanochemical activation of natural clay minerals: an alternative to produce sustainable cementitious binders – review». Mineralogy and Petrology (Springer) 113 (4): 449-462. Bibcode:2019MinPe.113..449T. doi:10.1007/s00710-019-00666-y.
- ↑ a b Jean-Pierre Bournazel; Yves Malier (1998). PRO 4: International RILEM Conference on Concrete: From Material to Structure. RILEM Publications. pp. 101-. ISBN 978-2-912143-04-4.
- ↑ a b c d e f g h Ronin, V (2010). An Industrially Proven Solution for Sustainable Pavements of High-Volume Pozzolan Concrete – Using Energetically Modified Cement, EMC. Washington DC, United States: Transportation Research Board of the National Academies.
- ↑ a b Humpreys, K.; Mahasenan, M. (2002). Toward a Sustainable Cement Industry Substudy 8: Climate Change. Geneva, Swtizerland: World Business Council for Sustainable Development (WBCSD).
- ↑ a b c Harvey, D (2013). Energy and the New Reality 1 – Energy Efficiency and the Demand for Energy Services. Taylor & Francis. ISBN 9781136542718.
- ↑ a b Kumar, Rakesh; Kumar, Sanjay; Mehrotra, S.P. (December 2007). «Towards sustainable solutions for fly ash through mechanical activation». Resources, Conservation and Recycling 52 (2): 157-179. doi:10.1016/j.resconrec.2007.06.007.
- ↑ a b Hasanbeigi, Ali; Price, Lynn; Lin, Elina (October 2012). «Emerging energy-efficiency and CO2 emission-reduction technologies for cement and concrete production: A technical review». Renewable and Sustainable Energy Reviews 16 (8): 6220-6238. S2CID 108511643. doi:10.1016/j.rser.2012.07.019.
- ↑ Hickenboth, Charles R.; Moore, Jeffrey S.; White, Scott R.; Sottos, Nancy R.; Baudry1, Jerome; Wilson, Scott R. (2007). «Biasing Reaction Pathways with Mechanical Force». Nature 446 (7134): 423-427. Bibcode:2007Natur.446..423H. PMID 17377579. S2CID 4427747. doi:10.1038/nature05681.(requiere suscripción)
- ↑ Carlier, Leslie; Baron, Michel; Chamayou, Alain; Couarraze, Guy (May 2013). «Greener pharmacy using solvent-free synthesis: Investigation of the mechanism in the case of dibenzophenazine». Powder Technology 240: 41-47. S2CID 97605147. doi:10.1016/j.powtec.2012.07.009.
- ↑ Živanović, Deana; Andrić, Ljubiša; Sekulić, Živko; Milošević, Siniša (1999). «Mechanical Activation of Mica». Advanced Science and Technology of Sintering. pp. 211-217. ISBN 978-1-4613-4661-6. doi:10.1007/978-1-4419-8666-5_29.
- ↑ Danny Harvey (12 de agosto de 2010). Energy and the New Reality 1:Energy Efficiency and the Demand for Energy Services. Routledge. pp. 385-. ISBN 978-1-136-54272-5.
- ↑ Eflgren, L.; Future Infrastructure Forum, Cambridge University (28 de marzo de 2013). Future Infrastructure Forum: Scandinavian Points of View.
- ↑ «Stipendieutdelning» (en sueco). Luleå tekniska universitet. 30 de agosto de 2006. Consultado el 24 de marzo de 2014.
- ↑ a b c d Colacino, Evelina; Garcia, Felipe (2023). Mechanochemistry and Emerging Technologies for Sustainable Chemical Manufacturing (en inglés) (1st edición). Routledge. p. 162. ISBN 9780367775018.
- ↑ Ronin, V.; Jonasson, J.E. (1993). New concrete technology with the use of energetically modified cement (EMC). Proceedings: Nordic Concrete Research Meeting, Göteborg, Sweden. Oslo, Norway: Norsk Betongforening (Nordic concrete research). pp. 53-55.
- ↑ LTU website. «Professor Lennart Elfgren». ltu.se.
- ↑ EUREKA. «EUREKA Gold Award for EMC Cement».
- ↑ Krishnaraj, L; Reddy, YBS; Madhusudhan, N; Ravichandran, PT (2017). «Effect of energetically modified Fly Ash on the durability properties of cement mortar». Rasayan Journal of Chemistry 10 (2): 423-428. doi:10.7324/RJC.2017.1021682.
- ↑ a b c d Hedlund, H; Ronin, V; Jonasson, J-E; Elfgren, L (1999). Grönare Betong [Green Cement] 91 (7). Stockholm, Sweden: Förlags AB Bygg & teknik. pp. 12-13.
- ↑ a b c d e f g h i Elfgren, L; Justnes, H; Ronin, V (2004). High Performance Concretes With Energetically Modified Cement (EMC). Kassel, Germany: Kassel University Press GmbH. pp. 93-102.
- ↑ a b United States Federal Highway Administration (FHWA). «EMC Cement Presentation January 18, 2011». Washington, DC.
- ↑ «Cement Data Sheet». U.S. Geological Survey. USGS. 2001. Consultado el 14 de agosto de 2020.
- ↑ «Cement Data Sheet». U.S. Geological Survey. USGS. 2020. Consultado el 10 de agosto de 2020.
- ↑ Energy Transitions Commission; Stern, Nicholas; Turner, Adair (2019). «Mission Possible sectoral focus: cement». Energy Transitions Commission. p. 15. Consultado el 1 de enero de 2022.
- ↑ Czigler, T; Reiter, S; Somers, K (May 2020). «Laying the foundation for zero-carbon cement». McKinsey & Co. Archivado desde el original el 19 de mayo de 2023. Consultado el 24 de agosto de 2020.
- ↑ USBR. «Hoover Dam Frequently Asked Questions and Answers». U.S. Bureau of Reclamation. Consultado el 10 de agosto de 2020.
- ↑ a b c d e f EMC Cement BV. Summary of CemPozz® (Fly Ash) Performance in Concrete. EMC Cement BV, 2012.
- ↑ Schneider, M.; Romer M., Tschudin M. Bolio C.; Tschudin, M.; Bolio, H. (2011). «Sustainable cement production – present and future». Cement and Concrete Research 41 (7): 642-650. doi:10.1016/j.cemconres.2011.03.019.
- ↑ a b c d Bache, M (1983). «Densified cement/ultra fine particle-based materials». Proceedings of the Second International Conference on Superplasticizers in Concrete.
- ↑ a b Chappex, T.; Scrivener K. (2012). «Alkali fixation of C-S-H in blended cement pastes and its relation to alkali silica reaction». Cement and Concrete Research 42 (8): 1049-1054. doi:10.1016/j.cemconres.2012.03.010.
- ↑ Private study, Luleå University of Technology (2001) "Diffusionstest för cementstabiliserad flygaska", LTU Rapport AT0134:01, 2001-09-03
- ↑ Ronin, V; Jonasson, J-E; Hedlund, H (1999). "Ecologically effective performance Portland cement-based binders", proceedings in Sandefjord, Norway 20–24 June 1999. Norway: Norsk Betongforening. pp. 1144-1153.
- ↑ a b Ronin, Vladimir; Emborg, Mats; Elfgren, Lennart (2014). «Self-Healing Performance and Microstructure Aspects of Concrete Using Energetically Modified Cement with a High Volume of Pozzolans». Nordic Concrete Research 51: 131-144 https://www.diva-portal.org/smash/record.jsf?dswid=-9911&pid=diva2%3A987595.
- ↑ Yang, Yingzi; Lepech, Michael D.; Yang, En-Hua; Li, Victor C. (May 2009). «Autogenous healing of engineered cementitious composites under wet–dry cycles». Cement and Concrete Research 39 (5): 382-390. doi:10.1016/j.cemconres.2009.01.013.
- ↑ Li, Victor C.; Herbert, Emily (28 de junio de 2012). «Robust Self-Healing Concrete for Sustainable Infrastructure». Journal of Advanced Concrete Technology 10 (6): 207-218. doi:10.3151/jact.10.207. hdl:2027.42/94191.
- ↑ Van Tittelboom, Kim; De Belie, Nele (27 de mayo de 2013). «Self-Healing in Cementitious Materials—A Review». Materials 6 (6): 2182-2217. Bibcode:2013Mate....6.2182V. PMC 5458958. PMID 28809268. doi:10.3390/ma6062182.
- ↑ a b c d e f g Justnes, Harald; Elfgren, Lennart; Ronin, Vladimir (February 2005). «Mechanism for performance of energetically modified cement versus corresponding blended cement». Cement and Concrete Research 35 (2): 315-323. doi:10.1016/j.cemconres.2004.05.022.
- ↑ a b Patent abstract for granted patent "Process for Producing Blended Cements with Reduced Carbon Dioxide Emissions" (Pub. No.:WO/2004/041746; International Application No.: PCT/SE2003001009; Pub. Date: 21.05.2004; International Filing Date: 16.06.2003)
- ↑ Moropoulou, A.; Cakmak, A.; Labropoulos, K.C.; Van Grieken, R.; Torfs, K. (January 2004). «Accelerated microstructural evolution of a calcium-silicate-hydrate (C-S-H) phase in pozzolanic pastes using fine siliceous sources: Comparison with historic pozzolanic mortars». Cement and Concrete Research 34 (1): 1-6. doi:10.1016/S0008-8846(03)00187-X.
- ↑ Moropoulou, A.; Cakmak, A.S.; Biscontin, G.; Bakolas, A.; Zendri, E. (December 2002). «Advanced Byzantine cement based composites resisting earthquake stresses: the crushed brick/lime mortars of Justinian's Hagia Sophia». Construction and Building Materials 16 (8): 543-552. doi:10.1016/S0950-0618(02)00005-3.
- ↑ a b EMC Cement BV. Summary of CemPozz® (Natural Pozzolan) Performance in Concrete. EMC Cement BV, 2012.
- ↑ a b c Stein, B (2012). A Summary of Technical Evaluations & Analytical Studies of Cempozz® Derived from Californian Natural Pozzolans. San Francisco, United States: Construction Materials Technology Research Associates, LLC.
- ↑ ACI 318 "Building Code Requirements for Structural Concrete and Commentary"
- ↑ a b Johansson, K; Larrson, C; Antzutkin, O; Forsling, W; Rao, KH; Ronin, V (1999). «Kinetics of the hydration reactions in the cement paste with mechanochemically modified cement 29Si magic-angle-spinning NMR study». Cement and Concrete Research (Pergamon) 29 (10): 1575-81. doi:10.1016/S0008-8846(99)00135-0. Consultado el 14 de agosto de 2020.
- ↑ a b c d e Baroghel Bouny, V (1996). Bournazel, J. P.; Malier, Y., eds. Texture and Moisture Properties of Ordinary and High Performance Cementitious Materials (in PRO 4: Concrete: From Material to Structure). 144 at 156: RILEM. p. 360. ISBN 2-912143-04-7.
- ↑ «Cement hydration». Understanding Cement.
- ↑ Thomas, Jeffrey J.; Jennings, Hamlin M. (January 2006). «A colloidal interpretation of chemical aging of the C-S-H gel and its effects on the properties of cement paste». Cement and Concrete Research 36 (1): 30-38. doi:10.1016/j.cemconres.2004.10.022.
- ↑ «Portlandite Mineral Data». www.webmineral.com.
- ↑ «Handbook of Mineralogy». rruff.geo.arizona.edu.
- ↑ Mertens, G.; Snellings, R.; Van Balen, K.; Bicer-Simsir, B.; Verlooy, P.; Elsen, J. (March 2009). «Pozzolanic reactions of common natural zeolites with lime and parameters affecting their reactivity». Cement and Concrete Research 39 (3): 233-240. doi:10.1016/j.cemconres.2008.11.008.
- ↑ Ca3Al2(SiO4)3−x(OH)4x, con hidróxido (OH) reemplazando parcialmente a la sílice (SiO4)
- ↑ Webmineral.com. «Stratlingite Mineral Data». Consultado el 6 de diciembre de 2013.. Véase también Ding, Jian; Fu, Yan; Beaudoin, J.J. (August 1995). «Strätlingite formation in high alumina cement – silica fume systems: Significance of sodium ions». Cement and Concrete Research 25 (6): 1311-1319. doi:10.1016/0008-8846(95)00124-U.
- ↑ Midgley, H.G.; Bhaskara Rao, P. (March 1978). «Formation of stratlingite, 2CaO.SiO2.Al2O3.8H2O, in relation to the hydration of high alumina cement». Cement and Concrete Research 8 (2): 169-172. doi:10.1016/0008-8846(78)90005-4.
- ↑ Midgley, H.G. (March 1976). «Quantitative determination of phases in high alumina cement clinkers by X-ray diffraction». Cement and Concrete Research 6 (2): 217-223. doi:10.1016/0008-8846(76)90119-8.
- ↑ Heikal, M.; Radwan, M M; Morsy, M S (2004). «Influence of curing temperature on the Physico-mechanical, Characteristics of Calcium Aluminate Cement with air cooled Slag or water cooled Slag». Ceramics-Silikáty 48 (4): 185-196.
- ↑ Abd-El.Aziz, M.A.; Abd.El.Aleem, S.; Heikal, Mohamed (January 2012). «Physico-chemical and mechanical characteristics of pozzolanic cement pastes and mortars hydrated at different curing temperatures». Construction and Building Materials 26 (1): 310-316. doi:10.1016/j.conbuildmat.2011.06.026.
- ↑ Mostafa, Nasser Y.; Zaki, Z.I.; Abd Elkader, Omar H. (November 2012). «Chemical activation of calcium aluminate cement composites cured at elevated temperature». Cement and Concrete Composites 34 (10): 1187-1193. doi:10.1016/j.cemconcomp.2012.08.002.
- ↑ Taylor, HFW, (1990) Cement chemistry, London: Academic Press, pp.319–23.
- ↑ Matusinović, T; Šipušić, J; Vrbos, N (November 2003). «Porosity–strength relation in calcium aluminate cement pastes». Cement and Concrete Research 33 (11): 1801-1806. doi:10.1016/S0008-8846(03)00201-1.
- ↑ Majumdar, A.J.; Singh, B. (November 1992). «Properties of some blended high-alumina cements». Cement and Concrete Research 22 (6): 1101-1114. doi:10.1016/0008-8846(92)90040-3.
- ↑ ASTM International (2010). «ASTM C989: Standard Specification for Slag Cement for Use in Concrete and Mortars». Book of Standards Volume 4 (2). doi:10.1520/c0989-10.
- ↑ Nhar, H.; Watanabe, T.; Hashimoto, C.; Nagao, S. (2007). Efflorescence of Concrete Products for Interlocking Block Pavements (Ninth CANMET/ACI International Conference on Recent Advances in Concrete Technology: Editor, Malhotra, V., M., 1st edición). Farmington Hills, Mich.: American Concrete Institute. pp. 19–34. ISBN 9780870312359.
- ↑ Boldyrev, V.V.; Pavlov, S.V.; Goldberg, E.L. (March 1996). «Interrelation between fine grinding and mechanical activation». International Journal of Mineral Processing. 44-45: 181-185. doi:10.1016/0301-7516(95)00028-3.
- ↑ Heinicke, G.; Hennig, H.-P.; Linke, E.; Steinike, U.; Thiessen, K.-P.; Meyer, K. (1984). «Tribochemistry: In Co-Operation with H.P. Hennig, et al.» [and with a preface by Peter-Adolf Thiessen]. Acta Polymerica (Berlin : Akademie-Verlag) 36 (7): 400-401. doi:10.1002/actp.1985.010360721.
- ↑ Unión Internacional de Química Pura y Aplicada. «Mechano-chemical reaction». Compendium of Chemical Terminology. Versión en línea (en inglés).
- ↑ Baláž, Peter; Achimovičová, Marcela; Baláž, Matej; Billik, Peter; Cherkezova-Zheleva, Zara; Criado, José Manuel; Delogu, Francesco; Dutková, Erika; Gaffet, Eric; Gotor, Francisco José; Kumar, Rakesh; Mitov, Ivan; Rojac, Tadej; Senna, Mamoru; Streletskii, Andrey; Wieczorek-Ciurowa, Krystyna (2013). «Hallmarks of mechanochemistry: from nanoparticles to technology». Chemical Society Reviews 42 (18): 7571-8137. PMID 23558752. S2CID 205853500. doi:10.1039/c3cs35468g. hdl:10261/96958.
- ↑ Smekal, A. (April 1942). «Ritzvorgang und molekulare Festigkeit». Die Naturwissenschaften 30 (14–15): 224-225. Bibcode:1942NW.....30..224S. S2CID 1036109. doi:10.1007/BF01481226.
- ↑ Hüttig, Gustav F. (1943). «Zwischenzustände bei Reaktionen im festen Zustand und ihre Bedeutung für die Katalyse». Heterogene Katalyse III. pp. 318-577. ISBN 978-3-642-52028-0. doi:10.1007/978-3-642-52046-4_9.
- ↑ Zelikman, AN; Voldman, GM; Beljajevskaja, LV (1975). Teorija Gidrometalurgiceskich Processov [Theory of hydrometallurgical processes] (en russian). Metallurgija.
- ↑ Meyer, K (1968). Physikalisch-chemische Kristallographie. VEB Deutscher Verlag für Grundstoffindustrie. p. 337. «(asin: B0000BSNEK)».
- ↑ a b Pourghahramani, P; Forssberg, E (March 2007). «Effects of mechanical activation on the reduction behavior of hematite concentrate». International Journal of Mineral Processing 82 (2): 96-105. doi:10.1016/J.MINPRO.2006.11.003.
- ↑ a b Pourghahramani, P; Forssberg, E (March 2007). «Reduction kinetics of mechanically activated hematite concentrate with hydrogen gas using nonisothermal methods». Thermochimica Acta 454 (2): 69-77. doi:10.1016/j.tca.2006.12.023.
- ↑ a b Pourghahramani, P; Forssberg, E (May 2006). «Comparative study of microstructural characteristics and stored energy of mechanically activated hematite in different grinding environments». International Journal of Mineral Processing 79 (2): 120-139. doi:10.1016/j.minpro.2006.01.010.
- ↑ a b Pourghahramani, P; Forssberg, E (May 2006). «Microstructure characterization of mechanically activated hematite using XRD line broadening». International Journal of Mineral Processing 79 (2): 106-119. doi:10.1016/j.minpro.2006.02.001.
- ↑ a b Pourghahramani, P; Forssberg, E (September 2007). «Changes in the structure of hematite by extended dry grinding in relation to imposed stress energy». Powder Technology 178 (1): 30-39. doi:10.1016/j.powtec.2007.04.003.
- ↑ a b Pourghahramani, P (2007). Mechanical Activation of Hematite Using Different Grinding Methods with Special Focus on Structural Changes and Reactivity (Tesis). p. 242.
- ↑ a b Tkáčová, K.; Baláž, P.; Mišura, B.; Vigdergauz, V.E.; Chanturiya, V.A. (July 1993). «Selective leaching of zinc from mechanically activated complex Cu-Pb-Zn concentrate». Hydrometallurgy 33 (3): 291-300. doi:10.1016/0304-386X(93)90068-O.
- ↑ Baláž, P (2000). Extractive metallurgy of activated minerals. Amsterdam: Elsevier Science B.V. p. 292. ISBN 9780080531533. Consultado el 21 de agosto de 2020.
- ↑ a b c d e Tkáčová, K. (1989). Mechanical activation of minerals. Amsterdam: Elsevier. p. 170. ISBN 978-0444988287.
- ↑ a b c d e Tromans, D.; Meech, J.A. (November 2001). «Enhanced dissolution of minerals: stored energy, amorphism and mechanical activation». Minerals Engineering 14 (11): 1359-1377. doi:10.1016/S0892-6875(01)00151-0.
- ↑ Nepapushev, A. A.; Kirakosyan, K. G.; Moskovskikh, D. O.; Kharatyan, S. L.; Rogachev, A. S.; Mukasyan, A. S. (2015). «Influence of high-energy ball milling on reaction kinetics in the Ni-Al system: An electrothermorgaphic study». International Journal of Self-Propagating High-Temperature Synthesis 24 (1): 21-28. S2CID 136668210. doi:10.3103/S1061386215010082.
- ↑ Ronin, V; Jonasson, JE (1994). Investigation of the effective winter concreting with the usage of energetically modified cement (EMC) - material science aspects, Report 1994:03, 24 pp. (en sueco). Luleå University (LTU), Div. of Struct Eng.
- ↑ Ronin, V; Jonasson, JE (1995). High strength and high performance concrete with use of EMC hardening at cold climate conditions. Proceedings of International Conference on Concrete under Severe Conditions, Sapporo, Japan, Luleå University (LTU), Div. of Struct Eng.
- ↑ Handle, Philip H.; Loerting, Thomas (2015). «Temperature-induced amorphisation of hexagonal ice». Physical Chemistry Chemical Physics 17 (7): 5403-5412. Bibcode:2015PCCP...17.5403H. PMID 25613472. doi:10.1039/C4CP05587J. Consultado el 21 de agosto de 2020.
- ↑ a b c d Sobolev, Konstantin (August 2005). «Mechano-chemical modification of cement with high volumes of blast furnace slag». Cement and Concrete Composites 27 (7–8): 848-853. doi:10.1016/j.cemconcomp.2005.03.010.
- ↑ Weichert, R.; Schönert, K. (1974). «On the temperature rise at the tip of a fast running crack†». Journal of the Mechanics and Physics of Solids 22 (2): 127-133. Bibcode:1974JMPSo..22..127W. doi:10.1016/0022-5096(74)90018-0.
- ↑ Fuller, K. N. G.; Fox, P. G.; Field, J. E. (1975). «The Temperature Rise at the Tip of Fast-Moving Cracks in Glassy Polymers». Proceedings of the Royal Society of London. Series A, Mathematical and Physical Sciences 341 (1627): 537-557. Bibcode:1975RSPSA.341..537F. JSTOR 78609. S2CID 137104796. doi:10.1098/rspa.1975.0007.
- ↑ a b Krycer, Ian; Hersey, John A. (November 1980). «A comparative study of comminution in rotary and vibratory ball mills». Powder Technology 27 (2): 137-141. doi:10.1016/0032-5910(80)85015-7.
- ↑ a b c d Venkataraman, K.S.; Narayanan, K.S. (May 1998). «Energetics of collision between grinding media in ball mills and mechanochemical effects». Powder Technology 96 (3): 190-201. doi:10.1016/S0032-5910(97)03368-8.
Enlaces externos
[editar]- Sitio web oficial , Suecia – en lowcarboncement.com
- Universidad Tecnológica de Luleå, Suecia – en LTU.se
- Future Infrastructure Forum, Universidad de Cambridge, Reino Unido – en Fif.construction.cam.ac.uk
- Estadísticas e información sobre cemento del Servicio Geológico de EE. UU. (USGS) – en Minerals.usgs.gov
- Agencia de Protección Ambiental de los EE. UU. (EPA), Información sobre las normas para la industria del cemento Portland – en EPA.gov
- Instituto Americano del hormigón – en Concrete.org
- EDGAR – Base de datos de emisiones para la investigación atmosférica global – en Edgar.jrc.ec.europa.eu
- Vitruvious: The Ten Books on Architecture en línea: texto en latín entrecruzado y traducción al inglés
- Iniciativa de Sostenibilidad del Cemento del WBCSD Archivado el 18 de diciembre de 2011 en Wayback Machine. – en Wbcsdcement.org