Niquelado químico
El niquelado químico es una técnica química auto-catalítica utilizada para depositar una capa de aleación níquel-fósforo o níquel-boro en una pieza de metal o plástico. El proceso es una reducción en fase acuosa y caliente, en la presencia de un agente reductor, por ejemplo: hipofosfito sódico hidratado (NaPO2H2·H2O), que reacciona con los iones metálicos para depositar el metal. La reacción es catalizada al inicio por el metal de la pieza y luego por el níquel depositado. Son posibles aleaciones con diferentes porcentajes de fósforo, desde 2-5 (bajo en fósforo) a un máximo de 11-14 (alto de fósforo). Las propiedades metalúrgicas de las aleaciones dependerán del porcentaje de fósforo.
El niquelado químico se caracteriza por un espesor de capa uniforme, incluso en piezas complicadas y en las superficies interiores. Además, las superficies se caracterizan por una dureza muy alta, una resistencia de salida buena, y protección contra la corrosión excelente. Los revestimientos químicos de níquel son soldables y, aunque el níquel es uno de los metales ferromagnéticos, el depósito no es ferromagnético. Las propiedades de la capa de un recubrimiento de níquel químico dependen de la pureza del material de base, el tratamiento previo y el espesor de la capa. En la mayoría de los métodos que se utilizan el contenido de fósforo está entre el 8,5 al 12%.
Información general
El niquelado químico es una reacción auto-catalítica utilizada para depositar un revestimiento de níquel sobre un sustrato. A diferencia de la galvanoplastia, no pasa una corriente eléctrica a través de la solución para formar un depósito. Esta técnica de recubrimiento es útil para evitar la corrosión y el desgaste. Esta técnica también se puede utilizar para la fabricación de revestimientos compuestos mediante la suspensión de polvo en el baño. Por ejemplo si se añade polvo de diamante se obtiene una buena superficie de lima y si se añade Teflón aumenta su lubricidad y resistencia a adherencia.
El niquelado químico posee varias ventajas frente a la galvanoplastia. Al estar libre de densidad de flujo y las cuestiones de suministro de energía, proporciona un depósito incluso independientemente de la geometría de la pieza. Con la correcta preparación de una capa catalizadora, se puede depositar en las superficies no conductoras.[1]
Resumen de la tecnología
En niquelado químico los depósitos se clasifican normalmente como recubrimientos funcionales e históricamente se han encontrado usos en aplicaciones que requieren de protección ya sea a la corrosión o al desgaste y en algunos casos, ambos. Debido a las propiedades únicas del depósito y la uniformidad de la película resultante, muchas otras aplicaciones han surgido que capitalizan la naturaleza multifuncional del níquel electrolítico. La mayoría de las películas de níquel utilizadas comercialmente son depositadas a partir de soluciones empleando hipofosfito sódico como agente reductor.[2] Esto da lugar a películas de níquel aleado con fósforo en oscila entre 1 y 12% en peso.
Las propiedades mecánicas de los depósitos de Ni+MP (PEV) pueden mejorarse aún más, no solo por la co-deposición de las partículas inertes tales como teflón, carburo de silicio o nitruro de boro, sino también mediante la aleación con un tercer elemento, formando una aleación ternaria de NiPX, donde X puede ser de cobre, tungsteno, molibdeno o estaño en función de la formulación particular. También mediante tratamiento térmico a temperaturas entre 280 y 440oC pueden lograrse incrementos de dureza notables por cambios en la micro estructura y precipitación de fosfuros de níquel. Cabe mencionar que antes del tratamiento térmico los depósitos con más de 10% de P son amorfos, por lo tanto, se consideran vidrio metálico lo cual reviste importantes implicaciones.
La aleaciones de níquel con boro (NIB) también aparecen en la literatura,[3] a pesar de que son menos viables comercialmente que las aleaciones de NiP. Las películas se generan utilizando borohidruro de sodio o dimetilaminoborano como agente reductor y puede variar su contenido en boro del 1 al 5 por ciento en peso. Las películas NiB se utilizan normalmente en la industria de la electrónica donde se requieren revestimientos de baja resistividad y también encuentran uso en aplicaciones industriales cuando se necesita un recubrimiento de extrema dureza y resistencia al desgaste.
El niquelado químico, al igual que el electrolítico, es tan fuerte como el eslabón más débil del proceso. Más claramente, el éxito niquelado químico requiere la adherencia estricta a las directrices de funcionamiento del baño y la preparación de la superficie óptima. Un proceso bien formulado de niquelado químico no supera una inadecuada preparación de la superficie. De forma análoga, aplicar el niquelado químico de forma incorrecta también dará un pobre recubrimiento aunque el sustrato está maravillosamente preparado.
Los siguientes enlaces son fundamentales:
- La preparación adecuada de la superficie
- Elección de níquel no electrolítico
- Conformidad con las Directrices de funcionamiento.
La incapacidad para reconocer la interconexión de estos tres elementos básicos en última instancia conduce a una insuficiencia en algún punto de la línea de fabricación.
Preparación de la superficie
Antes de realizar el niquelado químico, el material a tratar debe limpiarse con una serie de productos químicos, esto se conoce como el proceso de pre-tratamiento. Si no se consigue deshacerse de impurezas no deseadas el resultado de la superficie de la pieza será pobre. Cada pretratamiento químico debe ser seguido por un enjuague con agua (normalmente dos o tres veces) para eliminar los productos químicos que pueden adherirse a la superficie. El desengrasado elimina los aceites de la superficie, mientras que la limpieza con ácido elimina los óxidos e incrustraciones.
La activación se realiza con el mordido de un ácido débil, o un “toque” de níquel (aplicación breve de voltaje) o, en el caso de substrato no metálico, una solución de formulación patentada comercialmente o confidencial.
El pre-tratamiento requerido para la deposición de níquel y cromo sobre una superficie no conductora normalmente consiste en la preparación de la superficie inicial para hacer el sustrato hidrófilo. En algunos casos, como en el plástico ABS, se agrega un paso para disolver el butadieno presente en forma de partículas esferoidales dando lugar a una rugosidad de “anclaje”. Después de esta etapa inicial, la superficie es activada mediante una solución de un metal noble, por ejemplo, cloruro de paladio. También se utiliza nitrato de plata para activar el ABS y otros plásticos. El siguiente paso es la aplicación de la capa de níquel “electroless” cuya reacción es inducida y acelerada por las trazas de metal noble presentes del paso anterior. La formulación del baño autocatalítico varía según el activador. Después de esto, el sustrato ya estará listo para iniciar la deposición de níquel o cualquier otro metal mediante algún proceso electrolítico convencional.
Al finalizar el proceso de recubrimiento, las superficies chapadas deben ser tratadas con un anti-oxido o anti-deslustre químico como el fosfato trisódico o un cromato, seguido por un aclarado con agua para evitar manchas. El objeto enjuaguado entonces debe secarse completamente seca al horno para obtener la resistencia total de la película de recubrimiento.
Tipos
Aunque el níquel puede aparecer aleado con boro lo normal es el fósforo, y atendiendo a la concentración de este se distinguen tres grandes grupos:
Níquel químico con baja concentración de fósforo
Bajo tratamiento fósforo se aplica para los depósitos con dureza hasta 60 Rockwell C. Este tipo ofrece un espesor muy uniforme dentro de configuraciones complejas, así como fuera, que a menudo elimina molienda después de placas. También es excelente para la resistencia a la corrosión en ambientes alcalinos.[4]
Níquel químico con concentración media de fósforo
Tratamiento con fósforo medio tiene una tasa de velocidad de depósito de alto y ofrece opciones de brillantes y semi-brillante para la particularización cosmética. El tratamiento es muy estable, de uso frecuente para las industrias relativas a la eliminación de purín. Este es el tipo más común de níquelado químico.
Níquel químico con alta concentración de fósforo
De níquel electrolítico de alta fósforo ofrece resistencia a la corrosión, por lo que es ideal para los estándares de la industria que requieren protección contra ambientes ácidos altamente corrosivos, tales como la perforación de petróleo y la minería del carbón. Con microdureza que van hasta 600 VPN, este tipo asegura superficie muy poca porosidad donde se requiere pozo sin recubrimiento y no es propenso a las manchas. Los depósitos no son magnéticos cuando el contenido de fósforo es mayor que el 11,2%.[5]En cambio son difíciles de soldar.
Ventajas e inconvenientes
Las ventajas incluyen:
- No se utiliza energía eléctrica.
- Se puede lograr un recubrimiento uniforme en la superficie de las piezas.
- No hay plantillas sofisticadas o estantes.
- Hay flexibilidad en volumen de chapado y espesor.
- El proceso puede huecos y orificios ciegos con un grosor estable.
- Reposición química se puede controlar automáticamente.
- No se requiere un complejo método de filtrado.
- se puede obtener acabados mates, semibrillantes o brillantes.
Las desventajas incluyen:
- Vida útil de los productos químicos es limitado.
- El coste del tratamiento de residuos es alto debido a la rápida renovación química.
Cada tipo de níquel no electrolítico también tiene ventajas particulares dependiendo de la aplicación y el tipo de aleación de níquel.[6]
Propiedades físicas y mecánicas
Microestructura y composición de las películas de la NQP
Una de las ventajas del proceso de deposición no electrolítica de níquel es la capacidad para producir una aleación de níquel y fósforo en una composición variable. Dependiendo de la formulación y el funcionamiento la composición de película puede variar desde 2 hasta 13 por ciento en peso de fósforo[7]]. Esta variación en el contenido de la aleación tiene un efecto significativo sobre la microestructura de depósito y las características del rendimiento y ofrece flexibilidad para chapistas e ingenieros bien informados que pueden sacar el máximo provecho de estas diferencias.
El níquel electrodepositado tiene una pureza de más del 99% y esta altamente cristalino. Por otro contra, las deposiciones químicas de níquel que contienen más de 10,5% de fósforo parecen ser amorfas, es decir, carente de estructura cristalina.[8] Los depósitos ES con menos de 7 por ciento en peso de fósforo tienen una clara estructura microcristalina (2-6 nm tamaño de grano ) y las propiedades de la película son muy diferentes.[9] Algunos estudios han encontrado que el aumento de los depósitos de fósforo (fósforo por encima del 10,5 por ciento en peso), no puede ser verdaderamente amorfa, sino más bien una mezcla de microcristalina y fases amorfas.
Dejando de lado algunos de las características conocidas acerca de fósforo de depósito, es decir, la dureza o la resistencia a la corrosión que veremos un poco más tarde, los depósitos con un alto grado de composición amorfa están libres de los límites de grano, que por lo general actúan como sitios para la corrosión intergranular comúnmente encontradas en depósitos cristalinos. También hay aplicaciones que se benefician de la estructura cristalina. Duncan señaló que en la condición de un depositó de níquel no electrolítico[10] el revestimiento puede contener tanto las fases cristalinas y amorfas o sólo puede contener una. Cada fase ofrece distintos beneficios y la comprensión de lo que existe en el depósito es relevante para su utilización.[11]
Uniformidad


Una ventaja significativa del proceso de níquel no electrolítico es la capacidad de producir depósitos con un espesor uniforme en las piezas con geometrías y formas complejas.[12] Como se trata de una reacción química, cualquier catalizador superficie expuesta a la solución de metalización se placa de manera uniforme, que se adecue los criterios establecidos unos pocos párrafos antes. La densidad de corriente afecta típicamente asociados con galvanoplastia no son un factor, por lo tanto, los bordes afilados, rebajes profundos y agujeros ciegos son fácilmente chapada de espesor uniforme con la química de níquel no electrolítico. Muchas aplicaciones de níquel electrolítico existen hoy en día porque a menudo es la única forma de ciertos componentes de la placa. La diferencia en la uniformidad de depósito se ilustra en la figura 1. La figura 2 es una foto de golpes ES enchapadas en un flip chip, algo imposible de lograr con un depósito galvanizado.
El grado de uniformidad puede variar en los bordes, hilos, pequeños agujeros o huecos profundos donde el intercambio de una nueva solución puede ser difícil. Esto también puede ocurrir bajo condiciones con agitación baño excesivo, especialmente en la presencia de metales pesados.[13] Esta variación espesor puede ser controlado mediante la optimización de la dinámica de la solución o controlando la concentración de determinados aditivos formulados en el baño de chapado ES.
Punto de fusión

A diferencia de níquel electrodepositado, depósitos químicos de níquel no tiene un punto de fusión precisos sino que tienen un intervalo de fusión. El níquel puro tiene un punto de fusión de 1455 °C (2650 ° F), sin embargo ES es una aleación y como el contenido de fósforo se incrementa dentro de la película, el depósito comienza a ablandarse a temperaturas más bajas y continúa para ablandar hasta que eventualmente se derrite. El intervalo de fusión disminuye linealmente a medida que aumentan los niveles de fósforo. El punto de fusión eutéctico o menor para las aleaciones de NIP es 880 ° C (1620 ° F) y se produce con un contenido de fósforo depósito del 11% en peso.[14] El punto de fusión más alto es para los depósitos de fósforo bajo (menos de 3%) que tienen puntos de fusión a 1.200 ° C (2.200 ° F). Algunas aplicaciones de alta temperatura han fallado ya que no se reconoció plenamente que incluso con un alto un rango de la película todavía tendrá una fase líquida a temperaturas mucho más bajas. La Figura 3 ilustra lo que sucede se somete a temperaturas superiores a su punto de fusión.
Resistividad eléctrica

La resistividad eléctrica de las aleaciones de níquel químico es mayor que la de níquel puro. El níquel de alta pureza tiene una resistividad específica de 7,8 x 10-6 ohm-cm. Aumentando el contenido de fósforo aumenta la resistividad eléctrica de la película. (Figura 4). Los valores van desde 30-100 x 10-6 ohm-cm. El tratamiento térmico de la película PEV puede afectar la resistividad. A temperaturas tan bajas como 150 ° C la resistividad se reducirá debido a la liberación de hidrógeno absorbido físicamente. A temperaturas superiores a 250 ° C, una disminución similar marcado se producirá como resultado de la migración de fósforo y la transformación estructural de fosfuro de níquel.[15]
Propiedades magnéticas

Una aplicación importante del níquel químico es como una subcapa para los discos duros para computadoras. Para cumplir con los requisitos, el recubrimiento debe permanecer no magnético, incluso después de una hora de duración los ciclos de horneado de 250-300 ° C. En los últimos años, la industria de almacenamiento de datos ha elevado a la parte alta de este rango de temperaturas. Esto sólo se puede lograr con aleaciones alto contenido en fósforo (P> 10,5%) o con aditivos específicos. La propiedad no magnético de estas películas de fósforo es una de las características físicas más importantes.[16] La figura 5 muestra el efecto del contenido de fósforo sobre el ferromagnétismo.
No todas las aleaciones con alto contenido de fósforo mantienen el mismo nivel de estabilidad termomagnético. El rendimiento de la película también depende de la formulación química y la dinámica de la solución durante el proceso de recubrimiento. La reducción de la aparición y la velocidad de cristalización, lo que minimiza la fracción de volumen de microcristales y mantiene una estructura de grano homogénea a temperaturas más altas en el horno son requisitos clave para la optimización del rendimiento películas termomagnético.[17]
Resistencia a la corrosión
La aplicación más generalizada de la tecnología de níquel no electrolítico es proporcionar mayor protección contra la corrosión en una multitud de entornos corrosivos. Los datos del mercado indica claramente que el mayor uso del niquelado químico es sobre sustratos de acero y aluminio que son ánodos o menos noble que el níquel.[18] El niquelado químico actúa como un revestimiento de barrera que protege al proporcionar un revestimiento barrera libre de poros contra el ambiente corrosivo. Esto diferente de las películas consumibles formadas con zinc o aleación de zinc que proteger al material de base por sacrificar ellas.
La naturaleza del ambiente corrosivo y la resistencia al ataque químico son criterios importantes cuando se selecciona un determinado recubrimiento para un rendimiento óptimo. Los recubrimientos de alto contenido en fósforo (10.12%) son más fácilmente atacado en medios altamente alcalinos que de baja concentración de fósforo (1-3%). Sin embargo, los primeros resisten mucho mejor en un medio ácido.[19] Esto se ilustra en los siguientes gráficos.
Para optimizar el rendimiento de los recubrimientos ES de protección contra la corrosión se requiere que el recubrimiento sea continuo y libre de cualquier microporosidad, rugosidad, nódulos e irregularidades dentro de la microestructura. Dado que la microestructura de fósforo alto ES películas son amorfos son esencialmente libres de los límites de los granos que potencialmente podrían servir como sitios para la corrosión. La ausencia de límites de fase tales y la capacidad del fósforo alto ES película para formar una película pasiva en su superficie, lo convierten en una elección excelente para la protección de aluminio y acero sustratos altamente corrosivos, en ambientes ácidos.[20]
Sin embargo el contenido de fósforo solo no es suficiente para maximizar la resistencia a la corrosión del recubrimiento en un ambiente dado. Los factores que afectan el comportamiento de la corrosión de las películas de ES son las siguientes:
- 1. Adecuada selección del proceso de ES y el espesor de depósito.[21]
- 2. Operación y mantenimiento del proceso, minimizando depositados impurezas co-
- 3. Minimizar defectos del sustrato mediante la formación OEM mejora en la selección de sustrato (reparto vs extrusionado) y varias placas de pre-operaciones mecánicas (que forma, estampado, pulido, etc)
- 4. Selección del ciclo de pretratamiento óptimo
- 5. Operaciones Post placa (tanto buenas como malas). Bad-alta después del tratamiento de temperatura que pueden producir micro-depósitos-Bad agrietada. Buen post-salsas, hornea a baja temperatura, etc
El estado de la superficie juega un papel importante en la determinación del espesor del depósito requerido y rendimiento en el campo bueno. Por ejemplo, mecanizar sustratos aleados con azufre o plomo son particularmente vulnerables a un alto grado de porosidad, ya que estos componentes de aleación son venenos catalíticos en el proceso de deposición. Los sustratos con altos valores de rugosidad más gruesos requieren depósitos para proporcionar una protección adecuada a la corrosión. Esto se debe principalmente a la formación de nódulos durante las etapas iniciales de deposición, lo que deviene en una microporosidad de la película PEV.
El aumento del espesor de la película puede minimizar este efecto. Los sustratos lisos requieren un espesor de 25 micras para obtener una película con un mínimo de porosidad mientras que las superficies ásperas puede requerir hasta tres veces ese espesor para proporcionar protección contra una corrosión similar.[22]
El uso de pulverización de sal neutra, de acuerdo con la especificación ASTM B 117, para la medición de resistencia a la corrosión está bien documentado en la literatura y sigue siendo el método más ampliamente aceptado para la evaluación de un revestimiento.[23] Los resultados de la exposición de niebla salina neutra, contenido de fósforo y el espesor de depósito se resumen en la siguiente tabla:
Grosor del recubrimiento | 4-5% ENP | 7-8% ENP | 6.5-8% ENP | 10.5-12.0% ENP |
---|---|---|---|---|
12 microns (0.4 mils) | 24 | 24 | 24 | 250 |
22 microns (0.8 mils) | 96 | 96 | 96 | 1,000 |
38 microns (1.4 mils) | 96 | 96 | 96 | 1,000 |
50 microns (2.0 mils) | 96 | 96 | 96 | 1,000 |
Dureza de la película


La dureza de la película es una de las propiedades tribológicas clave de la tecnología de recubrimiento NQ. Los factores que afectan la dureza de película son: la composición (% P), la temperatura de tratamiento térmico y la curación de tratamiento térmico. Los valores típicos de microdureza están en la gana de 500 a 720 VHN (Figura 8). Esto contrasta con el níquel depositado electrolíticamente, que tienen valores típicos de 150 a 400VHN.[24]
El tratamiento térmico de la película aumenta significativamente la microdureza. La figura 9 ilustra el rango de temperatura efectiva y el tiempo requerido para alcanzar valores específicos.
En los casos en que el sustrato no puede soportar los requisitos de temperatura para alcanzar la máxima dureza, a menudo, se recomienda el empleo de baja concentración de fósforo. El aumento de la microdureza de películas se atribuye a las transformaciones de fases que tienen lugar durante el ciclo de calentamiento para formar níquel metálico y fosfuro de níquel. Se producirá algunos contracción de volumen y agrietamiento de la película y se debe tener en cuenta si la aplicación requiere protección contra la corrosión.
Resistencia al desgaste
El revestimiento químico de níquel y fósforo emplea en una amplia variedad de aplicaciones de ingeniería relacionadas con la resistencia al desgaste. Esto se debe principalmente al hecho de que los recubrimientos no sólo tienen alta dureza y lubricidad intrínseca, sino también proporcionar resistencia excelente a la corrosión y a la uniformidad de la película. Las propiedades de desgaste de las películas se puede mejorarse mediante la codeposición de partículas inertes, tales como PTFE, carburo de silicio o nitruro de boro formando un revestimiento compuesto.[22]

El desgaste por abrasión de las películas de la PEV se mide típicamente mediante la aplicación de una acción mecánica de un disco abrasivo, girando sobre la superficie chapada y midiendo la pérdida de peso (en miligramos) del recubrimiento a intervalos de 1000 ciclos. Esta prueba se conoce como el índice de desgaste Taber (IST). Y tal vez es el método utilizado más frecuentemente para evaluar las características de desgaste de las películas de la PEV.[25] Los resultados típicos de pérdida de peso de varias películas se ilustra en la Figura 10.
La razón por la cual los revestimientos de baja concentración de fósforo tienden a resistir el desgaste por abrasión mejor que de alta, se atribuye en gran medida a superiores valores de dureza. Sin embargo después del tratamiento térmico de las tendencias siguen siendo las mismos, aunque la dureza del depósito es similar, lo que sugiere que otros factores, tales como la composición de depósito, jugar un papel en la resistencia al desgaste abrasivo.
El desgaste adhesivo se define como la eliminación de material entre las superficies de contacto y mide la capacidad de resistir a las películas de soldadura por frotamiento, o agarrotamiento.[26] Si las superficies de contacto son de níquel no electrolítico, un rendimiento óptimo se logra cuando las superficies en contacto tienen propiedades diferentes, tales como contenido de fósforo o dureza. La resistencia al desgaste adhesivo de la Política Europea de Vecindad películas mejora con el contenido de fósforo en aumento.[27]
Es importante tener en cuenta tantas variables como sea posible en la evaluación de una política europea de vecindad para la capa de aplicaciones tribológicas. Factores tales como la dureza, contenido de fósforo, la presencia de líquidos o gases corrosivos, la temperatura, la naturaleza de la superficie de contacto, el grado de lubricación y las características del sustrato son críticas para el rendimiento óptimo.
Lubricidad

Como se señaló anteriormente, la lubricidad juega un papel importante en la optimización de la resistencia al desgaste. Lo hace por contacto entre la inhibición de las superficies de contacto, reduciendo la fricción y el calor asociado. Hard Chrome es bien conocido como poseedor de una película de la curación y auto lubricados. Considerando que la ES no presenta esta característica todavía ofrece una excelente lubricidad y encuentra muchas aplicaciones que pueden sacar provecho de esta propiedad.[28] La figura 11 muestra gráficamente el coeficiente de fricción vs no lubricado de acero. Cromo duro se desempeñan mejor que el estándar alto de fósforo ES (HP ES), pero con la oclusión de diversas partículas blandas que pueden alcanzar valores mucho más bajos.
La mayoría de los entornos de desgaste tienen múltiples puntos de contacto y es muy común que todas las superficies de contacto están chapados. La siguiente tabla muestra el mejor desempeño de níquel electrolítico cuando ambas superficies de contacto están chapados en que los resultados son comparables a las de cromo duro.
Mating Surface | Coeficiente de fricción | |
Sin lubricante | Lubricada | |
Electroless nickel vs Steel | 0.38 | 0.20 |
cromo vs acero | 0.21 | 0.13 |
acero vs acero | galling | 0.2 |
cromo vs cromo | 0.43 | 0.26 |
EN vs EN | 0.45 | 0.20 |
Elecroless nickel vs Cromo | 0.43 | 0.30 |
EN PTFE vs acero | 0.12 | |
EN Boron nitride vs acero | 0.07 |
Ductilidad
Aunque el níquel químico es ampliamente considerado como un revestimiento de ingeniería no se compara bien con otros recubrimientos en términos de ciertas propiedades mecánicas. La ductilidad es una de ellas. El níquel químico se considera un material muy fuerte pero frágil. La ductilidad relativamente baja se debe a las diversas estructuras microcristalinas y amorfa que limitan la deformación plástica,[29] es decir, la capacidad de "estirar" sin fractura. No es infrecuente que los depósitos pesados de generación (mayores de 25 micras) a agrietarse cuando se expone a cargas severas. Esto es especialmente evidente en las películas de fósforo de baja concentración o aquellos chapado de mayores baños (en exceso de 150 g / l de ortofosfato) con tensión de tracción alta.
Tensión interna



La tensión interna es sin duda una de las propiedades mecánicas más importantes de níquel electrolítico y, a menudo los más ignorados. La tensión interna juega un papel en la adhesión, la resistencia al desgaste y a la corrosión y por lo tanto deben ser regulados o, como mínimo, saber que existe. Las tensiones internas se pueden desarrollar tanto extrínseca y la intrínseca.
La tensión extrínseca es la menos insidiosa y es provocada por diferencias en el coeficiente de expansión térmica entre la película y el sustrato. Cuando las superficies chapadas se enfrió primero hay un encogimiento inherente al componente. Níquel electrolítico típicamente reduce aproximadamente 0,1% en refrigeración a partir de la temperatura del baño operativo. Cuando cultivaron sobre sustratos que tienen un mayor coeficiente de dilatación de ES (latón y aluminio, por ejemplo) el depósito ES se desarrollan esfuerzos de tracción. En los sustratos que tienen un menor coeficiente de dilatación que EN depósito de estar en un estado de compresión. Esto, por supuesto, no asume la pérdida de adhesión o agrietamiento grave como el componente pretende adaptarse a la contracción.
La tensión intrínseca es causada por el proceso de galvanizado en sí. Aunque el sustrato también juega un pequeño papel, la tensión intrínseca es controlada por la formación de las capas de níquel debido principalmente a la formulación ES y condiciones de operación del baño. Una observación general para orientar su proceso de pensamiento sería que el aumento de fósforo ES procesos efectuados de acuerdo con las buenas prácticas se producen depósitos con el estrés neutral o de compresión. En la mayoría de las aplicaciones, el esfuerzo de compresión se desea, ya que tiene un efecto insignificante sobre la pérdida de la fatiga, mejora la adhesión y algunas han encontrado una mejor protección a la corrosión. El gráfico de la figura 12 refleja la tensión de depósito frente a contenido de fósforo. Nótese que la reducción de fósforo (menos de 4% en peso) en la película también exhiben menor esfuerzo de tracción. Esto puede atribuirse a la presencia de fases homogéneas estructurales que Duncan observó.[30]
Suponiendo que se ha seleccionado la correcta formulación de ES para ofrecer el nivel de estrés deseado, una reducción de la tensión de compresión o incluso un cambio a la tracción es posible bajo ciertas condiciones y deben ser evitadas. El funcionamiento de un baño en fuera de sus directrices recomiendan afectará el estrés. Como Plater desea impulsar un proceso más rápido a la placa, aumentando el pH es a menudo la primera opción. Cuando se incrementa el pH el depósito de fósforo aumenta, el esfuerzo de compresión se reduce y esto puede conducir a resultados negativos.[31] Los chapistas se suelen sorprender al encontrar un proceso de chapado sin fisuras por tensión ni falta de adhesión, el día anterior, ahora está produciendo fallos. Una visión de los registros o un análisis rápido revela el culpable. El responsable más común para el aumento del carácter a tracción ES depósitos es la edad baño. Esta bien documentado que un proceso de ES diseñado para producir un depósito a la compresión deja de hacerlo después que el baño tenga de cierta edad (alrededor de unas 5 rotaciones de metal). Es en este punto donde la presencia de reacción de productos, ortofosfato de sodio, comienza a contribuir a la tracción. Se puede seguir empleando este baño, pero debe ser consciente de que la tensión aumentará y pueden aparecer fallos de adhesión o roturas. Esto es más evidente, de nuevo, con películas más gruesas. La figura 13 representa este fenómeno. Hay ciertos aditivos que, cuando se usa con cuidado, pueden reducir la tensión de tracción, incluso a medida que el baño en. Las fotos de la figura 14 corresponden a dos partes idénticas, recubiertas en el mismo baño, pero las edades del baño diferentes. La parte de la derecha se colocó en un baño relativamente nuevo mientras que la de la izquierda en un baño de casi 10 renovaciones de metal. Se habrá dado cuenta la clara evidencia de la descamación y la separación debido a la alta tensión interna.
Armado con una mejor comprensión de las propiedades de depósitos de níquel electrolítico de fósforo, ambos chapistas e ingenieros deben ser capaces de seleccionar eficazmente el proceso adecuado ES así como guías necesarias de funcionamiento para cada aplicación que se encuentran. La siguiente sección proporciona una visión general de estas aplicaciones.
Aplicaciones

El niquelado químico esta ganado aceptación en el mercado desde los anos 60 del siglo XX a través de una combinación de pruebas y errores, excelentes iniciativas de marketing y el compromiso de muchos pioneros de enchapado de tiendas dispuestas a tomar en una tecnología incipiente. Hoy en día, niquelado químico ofrece a la comunidad de ingeniería una tecnología fiable y diversa en el cumplimiento de diversos problemas de aplicación. Un desglose aproximado de aplicaciones en todo el mundo para el niquelado químico se detalla a continuación:
Automóvil
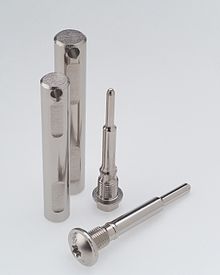

Esta industria saca el máximo provecho de las muchas ventajas que ofrece el niquelado químico. Las propiedades de la película tales como la uniformidad, la resistencia a la corrosión, la lubricidad y la resistencia al desgaste son razones por las que el uso en aplicaciones de automoción continúa creciendo. Históricamente, un segmento de mercado sensible al coste, los fabricantes de automóviles han adoptado el uso de los materiales de bajo coste chapados con una fina capa de niquelado químico para satisfacer los estrictos requisitos de una manera económica. Los sistemas de inyección de combustible, filtros de combustible de aluminio, pasadores de freno y las válvulas de escape son sólo unas pocas aplicaciones que aprovechan al máximo la resistencia a la corrosión de la película. Los ejes diferenciales de piñón y una variedad de pasadores y arandelas están chapados en grandes cantidades de revestimientos debido a la lubricidad, propiedades de resistencia al desgaste y anti-gripaje(Figura 15). Los pistones de freno están recubiertos en níquel no electrolítico brillante, con una riqueza madia de fósforo y tratados térmicamente para aumentar la dureza y resistencia al desgaste. En los pistones se emplean gruesos depósito brillantespara mejora el acabado superficial y obtener una menor fricción (Figura 16). Los yugos de hierro deslizantes se recubren para eliminar el ruido asociado con el gripado.
Las futuras aplicaciones más probable es que incluyen el uso de materiales compuestos ES como PTFE, nitruro de boro y carburo de silicio. El uso y el crecimiento de la tecnología de pila de combustible en los automóviles se muestra prometedor y níquel podría desempeñar un papel importante. La ES se enfrentó con un desafío cuando entró en vigor la Directiva sobre el final de la Vida del Vehículo (ELV)[32] que prohíbe el uso de varios metales tóxicos a menudo se encuentran en los depósitos ES. Cuando se promulgó se consideró como una barrera, pero muchos expertos consideran que la Directiva de VFU y otras iniciativas ecológicas similares han hecho avanzar la tecnología ES.
Aeroespacial
Los ingenieros de diseño han encontrado que la combinación de las propiedades funcionales de níquel químico son muy atractivas para su uso aeroespacial. Debido a los problemas de fiabilidad obvios asociados con este segmento de mercado, a largo plazo, la evaluación, a fondo de níquel electrolítico ha estado en marcha y ha realizado un lento progreso. El éxito de las pruebas y la solicitud de un número de años dio lugar a una mejor comprensión de cuándo y cómo utilizar el níquel no electrolítico. Su empleo en los montajes de motor, servoválvulas, tren de aterrizaje, álabes de turbina y similares han encontrado un uso extendido. A diferencia de cromo duro, hizo hincapié en la compresión depósitos altos de fósforo no reducen significativamente la resistencia a la fatiga de los componentes críticos. Por esta razón y razones expuestas anteriormente, parece seguro que continuara ampliando su uso.[33]
Electrónica



El uso de níquel electrolítico para aplicaciones electrónicas sigue creciendo y es sin duda el segmento de mercado más diverso. Las propiedades magnéticas, la resistencia a la corrosión y soldabilidad son las características que más han contribuido a su éxito.
Se utiliza ampliamente en la fabricación de unidades de disco duro (Figura 17), como una forma de proporcionar un revestimiento atómicamente liso en los discos de aluminio, las capas magnéticas se deposita entonces en la parte superior de esta película, usualmente por pulverización y el acabado con carbono y capas de protección de lubricación. Estas dos últimas capas proteger la capa subyacente magnética de avería de la cabeza de lectura / escritura si pierde su cojín de aire y entra en contacto con la superficie. La uniformidad, no magnético de carácter suave y fiable, la naturaleza libre de defectos prestan a su uso continuado.
Los disipadores de calor, los semiconductores, paquetes y componentes para las baterías, son ejemplos de otras aplicaciones electrónicas de alto volumen con níquel no electrolítico (Figura 18). P.e. una matriz de conectores de aluminio y zinc fundido recubiertos con níquel para mejorar la resistencia al desgaste y la corrosión (Figura 19). La uniformidad, conductividad eléctrica y soldabilidad son propiedades importantes para esta aplicación.
Un área de interés y crecimiento es el revestimiento de componentes de microondas. Con formas complejas y profundas zonas rebajadas níquel no electrolítico es ideal para actuar como una película de barrera resistente a la corrosión en la parte superior de aluminio y por debajo de la plata o capa final estaño electrolíticamente.
A pesar de ciertos obstáculos técnicos debe ser superado, el uso de níquel electrolítico de fósforo por debajo de medio de oro de inmersión en placas de circuitos, se muestra prometedor. Comúnmente conocido como el ENIG ( oro electrolítico inmersión níquel ) proceso, que ofrece una mejor vida útil en condiciones de humedad y mantiene excelente soldabilidad durante períodos de almacenamiento a largo. La energía renovable también parece ofrecer una promesa para ES en su uso para la metalización las células fotovoltaicas, se está desarrollando rápidamente.
Tratamiento químico
Los requisitos para esta aplicación incluyen a menudo la necesidad de mantener la pureza del producto, además de las necesidades típicas para la uniformidad y resistencia a la corrosión. La selección del níquel químico adecuado es a menudo crucial para una aplicación con éxito. Estudios recientes han encontrado el contenido de fósforo juega un papel importante en el rendimiento general del depósito de ES en un entorno específico. Bombas, válvulas y bridas son normalmente recubiertas con 50-100 micras de níquel no electrolítico para aplicaciones muy severas.
Industria de petróleo y del gas
Un campo de pruebas para níquel no electrolítico en los últimos 25 años, el éxito de níquel electrolítico de estas aplicaciones está bien documentado. Las válvulas de bola, intercambiadores de calor, bombas, etc. fabricados con materiales menos costosos y recubiertos con el fósforo de alta ES ha contribuido en gran medida al éxito. La resistencia a la corrosión en ambientes agresivos y la resistencia al desgaste, así como su uniformidad permitirá ES para mantener su posición dominante en este segmento del mercado.[34]
Otras aplicaciones


Manipulación de alimentos, la protección del molde, herramientas de fundición, placas a los no conductores y la industria de la impresión son algunas otras aplicaciones donde se encuentra el uso de níquel electrolítico significativo. Aplicaciones textiles (Figura 20) utilizan una excelente resistencia al desgaste y las características de lubricidad. Recubrimientos con materiales compuestos, tales como el nitruro de ES / boro han encontrado un mayor uso en aplicaciones que requieren extender la vida de servicio (Figura 21).
La forma más común de niquelado químico produce un revestimiento de aleación fósforo y níquel. El contenido de fósforo en los recubrimientos de níquel no electrolítico puede variar del 2% al 13%.[6] Se utiliza comúnmente en aplicaciones de revestimiento de ingeniería donde se requiere resistencia al desgaste, dureza y protección contra la corrosión. Las aplicaciones incluyen válvulas de campos petroleros, rotores, ejes de transmisión, equipos de manejo de papel, barras de combustible, superficies ópticas para torneado con diamante, las perillas de las puertas, utensilios de cocina, accesorios de cuarto de baño, los eléctricos / mecánicos herramientas y equipo de oficina. También se usa comúnmente como un recubrimiento en la electrónica de placa de circuito impreso de fabricación, típicamente con una superposición de oro para evitar la corrosión. Este proceso se conoce como oro electrolítico de níquel inmersión.
Debido a la alta dureza del recubrimiento se puede utilizar para recuperar piezas desgastadas. Se puede aplicar recubrimientos de 25 a 100 micrómetros y mecanizarlos de nuevo a las dimensiones finales. Su perfil deposición uniforme significa que se puede aplicar a los componentes de complejos no fácilmente adaptadas a otros recubrimientos duros que usan como el cromo duro.
La siguiente tabla ofrece una guía general para seleccionar un níquel no electrolítico para una aplicación específica o requisito:
Aplicación o característica
deseada de la película |
contenido bajo P
(1-3% b.w.) |
contenido medio-bajo P
(4-6% b.w.) |
Contenido medio P
(7-9% b.w.) |
Contenido alto P
(10.5-12% b.w.) |
EN con PTFE
EN con nitrato de boro |
EN con Carburo de silicio
EN con diamante |
---|---|---|---|---|---|---|
Moderada resistencia al desgaste | ▲ | ▲ | ▲ | ▲ | ▲ | |
Fuerte resistencia al desgaste | ▲ | |||||
Resistencia a la corrosión
según ASTM B117 |
▲ | |||||
Soldabilidad | ▲ | ▲ | ||||
Exposición a alta temperatura | ▲ | |||||
fricción baja | ▲ | |||||
Resistencia química (ácido) | ▲ | |||||
Resistencia química (base) | ▲ | ▲ | ||||
Brillo | ▲ | ▲ | ||||
Torneado con diamante | ▲ | |||||
Sin magnetísimo | ▲ |
Normas
- MGA-2404
- AMS-C-26074
- ASTM B-733
- ASTM-B-656
- MIL-DTL-32119
Véase también
Referencias
- ↑ Electroless Nickel Plating & Coating Services - Electro-Coatings
- ↑ Electroless Nickel Plating - A Guide
- ↑ http://www.thomasnet.com/southern-california/plating-electroless-nickel-boron-nitride-95923496-1.html
- ↑ http://corrosion-doctors.org/MetalCoatings/Electroless.htm
- ↑ ASTM B733 - 04(2009) Standard Specification for Autocatalytic (Electroless) Nickel Phosphorus Coatings on Metal
- ↑ a b Fact sheet on Electroless Nickel
- ↑ https://web.archive.org/web/20120328051147/http://www.valkro.com/AnodizingandElectrolessNickel/ElectrolessNickelPlating
- ↑ http://docs.google.com/viewer?a=v&q=cache:GtS9xKb6foYJ:www.rsp-technology.com/Fraunhof-Spie-Astronomics-2010.pdf+10.5+percent+phosphorous+nickel+electroless+amorphous&hl=fr&gl=fr&pid=bl&srcid=ADGEESj5_YwWv20zVvVELGcuvqWlYus19xzJZv1gEU5QXZHGmN6vHJfKsvfkTw_I-hRsIMDv3XJX6qwUHjCZo0tZ9GjEOsGhhH9hiT2qzDPTi2ojhsTuTyFxEEbVDFHu4yFijzaphFy-&sig=AHIEtbTk3bsFACcEQBuvO-Z4g9M8n73zsw
- ↑ http://docs.google.com/viewer?a=v&q=cache:9zY4lTWDRQ8J:uqu.edu.sa/files2/tiny_mce/plugins/filemanager/files/4300270/1/2/3/4/5/6/8/9/4.%2520The%2520Properties%2520of%2520Electroless%2520Nickel%2520Plating.pdf+10.5+percent+phosphorous+nickel+electroless+crystalline&hl=fr&gl=fr&pid=bl&srcid=ADGEESis627ocXTE_yK3W_fODztcsvPP9xg8wmGoeaLB57BlzsemiaZ2dWwMRrTWmfLmCIW9yTixXJf1K962ofrQsDqwwyBOnhdoRQnHOHH6IJ0BOyscsT-kWqTdrGtSu31FcvIAYNLc&sig=AHIEtbT46UpRBr4h4Ak9zCHJfj0NAzDN0g
- ↑ http://www.coventya.com
- ↑ http://www.sciencedirect.com/science/article/pii/S0257897203007461
- ↑ http://www.sciencedirect.com/science/article/pii/025789729190140R
- ↑ http://www.sciencedirect.com/science/article/pii/S002605760580844X
- ↑ http://www.finishingtalk.com/community/post93.html
- ↑ http://www.springerlink.com/content/u544534w11642011/
- ↑ http://docs.google.com/viewer?a=v&q=cache:aRiHLkMTCagJ:www.stapletontech.com/pdf_files/sos.pdf+remain+non+magnetic+electroless+nickel+high+phosphorous+alloys+heat+%3E10.5&hl=fr&gl=fr&pid=bl&srcid=ADGEESgYr389wXoru5fSeL_8kihu7m2nU8Vdt0blbHpP0_telsLkCzcf3Ido7eptqj9ar73sT_FHKXG7942Q5YO-3ly7qMhGLbq0hb7S9bisb6orIJDe4otgEHQJKo0ckYaxdh7zPfr8&sig=AHIEtbQ-9oQiv7hqo8i0Scrhl8T8BnX6BQ
- ↑ «Copia archivada». Archivado desde el original el 20 de marzo de 2012. Consultado el 21 de abril de 2016.
- ↑ http://www.surfacetechnology.co.uk/electroless-nickel/
- ↑ http://www.poeton.co.uk/electroless-nickel.htm
- ↑ https://web.archive.org/web/20121024031359/http://www.ingentaconnect.com/content/maney/se/2002/00000018/00000005/art00004
- ↑ «Copia archivada». Archivado desde el original el 27 de marzo de 2012. Consultado el 21 de abril de 2012.
- ↑ a b «Copia archivada». Archivado desde el original el 8 de mayo de 2016. Consultado el 21 de abril de 2016.
- ↑ http://www.astm.org/Standards/B117.htm
- ↑ http://docs.google.com/viewer?a=v&q=cache:vj_bT-SXpUkJ:www.twincityplating.com/resources/27Comparison%2520of%2520Electroless%2520vs.%2520Electrolytic%2520Nickel%2520Deposits.pdf+150+400+VHN+electroless+nickel&hl=fr&gl=fr&pid=bl&srcid=ADGEESgSaDtxva6tayCvYGX7brKsIXUaUOCIlHlWMf-D1TqpQZWBrDvbaCdgiBdLFklvdNNETF2Su-8SmKH2bXpNi4zHulXcxb9pgZq6c-TB71TFzfNzT3RdilcVwidEkHwQ-IS9lvVq&sig=AHIEtbTVGuI1G5TNch9vP7gk6sjT85G5bw
- ↑ http://docs.google.com/viewer?a=v&q=cache:yO2khws_KxsJ:www.angelfire.com/electronic2/elnp/reports.doc+taber+wear+index+characteristic+ENP&hl=fr&gl=fr&pid=bl&srcid=ADGEESgBSblxMNNB2U1DfwYIWliv99st8_d9DiOzb426wZHSfS0fRtdD3GkJtewIdb5B3FlSVrMJ6LQQWe64c1xwxsbGV-a5BxcDxF2XPPkykdv6YG27MtfA0kHc_TcVEEdJaTC2mag7&sig=AHIEtbRyGUkrfIeyzHAXf1R2DbvHwiA6gg
- ↑ https://web.archive.org/web/20111005064908/http://www.cyberbeach.net/lberta/oillubdc.html
- ↑ http://docs.google.com/viewer?a=v&q=cache:yO2khws_KxsJ:www.angelfire.com/electronic2/elnp/reports.doc+The+adhesive+wear+resistance+of+ENP+films+improves+with+increasing+phosphorous+content.&hl=fr&gl=fr&pid=bl&srcid=ADGEESgBSblxMNNB2U1DfwYIWliv99st8_d9DiOzb426wZHSfS0fRtdD3GkJtewIdb5B3FlSVrMJ6LQQWe64c1xwxsbGV-a5BxcDxF2XPPkykdv6YG27MtfA0kHc_TcVEEdJaTC2mag7&sig=AHIEtbTQbNd3No6XYTeYJDOGaon36taoZg
- ↑ «Copia archivada». Archivado desde el original el 13 de enero de 2012. Consultado el 26 de julio de 2011.
- ↑ http://docs.google.com/viewer?a=v&q=cache:9zY4lTWDRQ8J:uqu.edu.sa/files2/tiny_mce/plugins/filemanager/files/4300270/1/2/3/4/5/6/8/9/4.%2520The%2520Properties%2520of%2520Electroless%2520Nickel%2520Plating.pdf+The+relatively+low+ductility+is+due+to+the+various+microcrystalline+and+amorphous+structures+pointed+out+earlier+that+limits+plastic+deformation&hl=fr&gl=fr&pid=bl&srcid=ADGEESis627ocXTE_yK3W_fODztcsvPP9xg8wmGoeaLB57BlzsemiaZ2dWwMRrTWmfLmCIW9yTixXJf1K962ofrQsDqwwyBOnhdoRQnHOHH6IJ0BOyscsT-kWqTdrGtSu31FcvIAYNLc&sig=AHIEtbRupYvnZomkbkc3i-f7JpgAojD6PQ
- ↑ http://www.sciencedirect.com/science/article/pii/S0040609000008592
- ↑ http://docs.google.com/viewer?a=v&q=cache:Ed-BQ-NldBkJ:www.tau.ac.il/~chemlaba/Files/Electroless/12777_02.pdf+When+the+pH+is+increased+the+deposit+phosphorus+drops,+compressive+stress+is+reduced+and+this+can+lead+to+negative+results&hl=fr&gl=fr&pid=bl&srcid=ADGEESg-lZe_G337GONjGRUL0yjs_CLOBC4p_xQ7CK62tj8aOgluxi4jCBj-pbFfUJ35RZ2yWNLf5rffj9co-UIxKEHnxJB9PNAcZARSJOUikkMRdWALG8sF6m2Lf8VUO0HB70lTnoP7&sig=AHIEtbRbQSpB85nftXsVYDOFrViORwFOVA
- ↑ http://rod.eionet.europa.eu/instruments/526
- ↑ http://www.coventya.com/
- ↑ http://www.coventya.com/?pid=305&a=2&b=2&c=457&d=18